Effective
supply chain management is fundamental to the success of any eCommerce operation, and selecting the appropriate warehouse type plays a crucial role. The article provides an in-depth examination of 11 key warehouse types—including public, private, bonded, smart, and fulfillment centers—detailing their unique characteristics, benefits, and ideal use cases. By understanding these warehousing options, your business can significantly enhance operational efficiency, improve
customer satisfaction, and sustain competitive advantage.
1. Public Warehouses
Public warehouses are storage facilities available for rent by any company or individual. Often run by
third-party logistics (3PL) providers or government agencies, these warehouses offer space and services to multiple clients on a short-term or long-term. For example, a startup eCommerce retailer with fluctuating inventory can lease space in a public warehouse instead of investing in its own facility. It makes public warehousing a cost-effective option for small to medium businesses that need flexible storage.
Public warehouses typically handle
warehousing in logistics for various clients under one roof, so they provide basic storage and sometimes additional services like
inventory management or shipping. They allow businesses to
scale storage on demand – you pay for the space and time you need without large capital expenditure. This flexibility is a major advantage, as it frees up capital and
reduces the burden of managing a warehouse in-house. Many 3PL-run public warehouses also leverage their combined client volumes to negotiate better
shipping rates, which can benefit smaller.
However, the trade-off is that with public warehousing you have
less control. The facility and operations are managed by the provider, and the environment is often “standard” to accommodate all clients. Public warehouses may offer only basic infrastructure – for instance, fewer customization options or limited integration with a client’s systems. If your business requires specialized handling or a sophisticated
Warehouse Management System (WMS), a generic public warehouse might not meet all your needs. Despite this, public warehouses remain popular for businesses that need
affordable, flexible warehousing without long-term commitments. Many 3PL companies (including international providers offering warehousing services in China) make it easy for eCommerce sellers to get started with minimal upfront cost.
2. Private Warehouses
Private warehouses (also known as proprietary warehouses) are owned or operated by a single company for their exclusive use. These are often built or leased by large retailers, manufacturers, or distributors who have consistent, high-volume storage needs. Private warehousing gives a company complete control over storage conditions, inventory management, and warehouse operations. For example, a big-box retailer might operate private regional warehouses to feed products to its stores and online customers with maximum control over the supply chain.
Because they are dedicated to one business, private warehouses can be
optimized for that company’s specific needs. The owner can implement custom
layouts, technology systems, and processes that align with their products and fulfillment strategies. The high degree of control is a key benefit – companies can ensure the warehouse operates in lockstep with their overall logistics strategy and brand requirements. Private warehouses also allow a business to expand capacity and configure the space as it sees fit (for example, adding automation, climate control, or special security measures for high-value goods).
The downside, however, is
cost. Establishing and maintaining a private warehouse requires significant
capital investment – purchasing or leasing the building, outfitting it with equipment, and hiring staff. This is why private warehouses are typically used by larger companies that can achieve economies of scale with high volume. Small businesses usually find private warehousing prohibitively expensive. Additionally, running a private warehouse means the company bears all the
operational costs and risks: if space is underutilized or
inventory turnover is slow, the fixed costs still accrue. There’s also less flexibility to relocate or scale down quickly, since you may be tied to owned real estate or long leases.
3. Bonded Warehouses
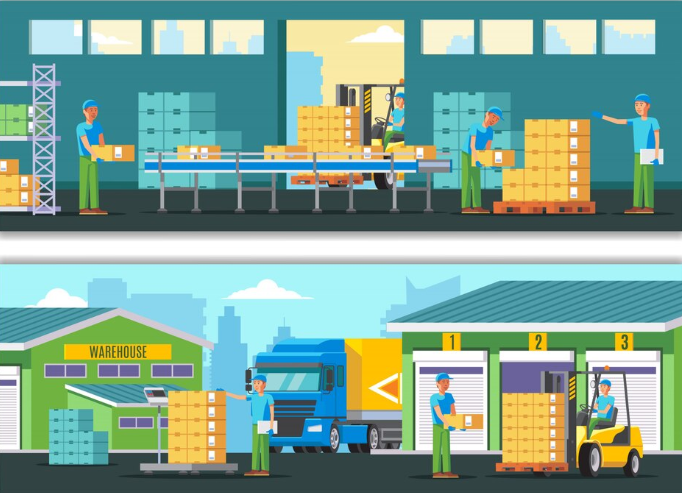
Bonded warehouses (customs bonded warehouses) are specialized storage facilities where imported goods can be stored without immediate payment of import duties or taxes. These warehouses operate under the supervision of customs authorities. Importers use bonded warehouses to defer duty payments until their goods are ready to be released into the market or re-exported. It is particularly useful for international eCommerce businesses and import/export companies.
In a bonded warehouse, goods are kept in bond – hence the name – which means the owner provides a customs bond (guarantee) to the government. While in storage, the goods are under customs control and cannot enter the domestic market without clearance. One key advantage of bonded warehousing is improved cash flow management for importers. You can store products for months or even years (in the US, up to 5 years) without paying duties upfront. It is ideal if you have inventory that might be sold gradually or needs to wait for compliance checks. It’s also useful for seasonal goods – you can import when convenient, hold in bond, and only pay duties when you actually distribute the goods domestically.
Bonded warehouses often provide value-added services under customs supervision, such as repackaging, labeling, or light assembly of the goods, as long as these processes don’t amount to full manufacturing. For example, an importer of electronics might store items in a bonded facility and relabel them for different countries’ requirements before final distribution. If the goods are re-exported from the bonded warehouse to another country, no import duty is paid at all in the storage country simplifying re-exporting and transshipping operations.
Using a bonded warehouse does involve working closely with customs and following regulations. The warehouse must be an approved facility and there may be administrative paperwork to account for goods upon entry, storage, and exit. Additionally, while duties are deferred, there may be storage fees and the cost of maintaining the customs bond. Nonetheless, bonded warehouses are an integral part of global supply chain warehousing for companies that deal with international shipments, providing tax and cash-flow advantages for importers.
4. Distribution Centers
A
distribution center (DC) is a type of warehouse focused not just on storage but on the rapid movement of goods to retailers or consumers. Distribution centers are
high-efficiency hubs in the supply chain, designed to receive products in bulk, then
turn them around quickly as outgoing orders. Unlike a basic storage warehouse, a distribution center typically handles
order fulfillment processes such as picking items, packing shipments, and managing inventory turnover on a short timeline. They are a key link between suppliers or manufacturers and the end customers (or retail stores).
In practical terms, distribution centers are customer-oriented facilities. For example, an eCommerce business might use a distribution center near a major market to ensure 1-2 day deliveries. When inventory arrives at the DC, it’s checked and shelved briefly, but soon after, customer orders are processed: items are picked from shelves, packaged, and shipped out, often within the same day or within a few days. It means products don’t sit in a distribution center for long – short-term storage with high velocity is the norm. As a result, distribution centers prioritize efficient layout, advanced warehouse management systems, and sometimes automation to handle large volumes of incoming and outgoing orders.
Distribution centers often provide additional services beyond storage, such as quality control, kitting/assembly, and handling returns. Many are operated by third-party logistics providers as shared facilities, while large retailers (like Amazon or Walmart) operate their own vast networks of distribution centers. Because they’re all about throughput, DCs might also incorporate cross-docking operations (direct transfer from inbound to outbound, see below) and consolidation of shipments from multiple sources. Essentially, a distribution center is a specialized warehouse that serves as a fulfillment engine, linking upstream supply (manufacturers, wholesalers) with downstream demand (retail stores or online consumers).
It’s worth noting the distinction between a distribution center and a regular warehouse: while all distribution centers are warehouses, not all warehouses are distribution centers. A traditional warehouse might store goods for months; a distribution center is characterized by
fast inventory turnover and value-added services. Modern distribution centers use technologies like conveyor systems, barcode/
RFID tracking, and real-time inventory management to handle goods efficiently. In eCommerce, partnering with a capable distribution center or 3PL provider can greatly improve your
order fulfillment speed and reduce shipping costs by positioning inventory closer to customers. (For insight on this, see our guide on the differences between warehouses and distribution centers on SendFromChina's blog.)
5. Smart Warehouses
(A modern distribution facility equipped with automated sorting conveyors. Smart warehouses use technologies like this to streamline the movement of goods.)
Smart warehouses represent the cutting-edge of warehousing in logistics. These facilities leverage
advanced technology and automation – such as robotics, artificial intelligence, Internet of Things (IoT) sensors, and sophisticated software – to optimize nearly every aspect of warehouse operations. In a smart warehouse, many traditional manual processes are automated: autonomous mobile robots might handle picking and packing, conveyor systems and drones move inventory, and AI-driven software manages
inventory levels and routes orders to the best location.
In essence, a smart warehouse is a highly automated fulfillment center designed for maximum efficiency. For example, imagine a warehouse where as soon as an online order comes in, a
warehouse management system assigns a robot to pick the item from storage, while conveyors route the item to a packing station, and an automated label printer prepares the
shipping label. Sensors track inventory in real time, updating stock counts as items are picked or replenished. Such a system can significantly
speed up order processing and reduce errors, handling large volumes of orders with minimal human intervention.
Key technologies found in smart warehouses include:
Automated storage and retrieval systems (AS/RS) – robots that store and retrieve pallets or bins from high racks.
Automated Guided Vehicles (AGVs) or Autonomous Mobile Robots (AMRs) – machines that transport goods within the warehouse without human drivers.
Advanced WMS and data analytics – software that uses data to optimize inventory placement, predict demand, and route orders efficiently.
IoT sensors – devices monitoring conditions (like temperature, humidity) or tracking assets to provide real-time visibility.
Machine learning/AI – for demand forecasting, labor scheduling, and even adjusting warehouse climate controls intelligently.
The benefits of a smart warehouse include dramatically improved efficiency, accuracy, and scalability. Because many tasks are automated, the warehouse can operate around the clock with fewer labor constraints, and scale up during peak seasons by simply increasing the throughput of machines. Error rates in picking and inventory counts drop with systems that double-check via scanners and sensors. In fact, these intelligent warehouses create a data-driven ecosystem where every movement is tracked and optimized.
Of course, smart warehousing comes with a high initial investment – advanced systems are expensive to implement. They make the most sense for large-scale operations (like major eCommerce fulfillment centers or high-volume distribution hubs) where even small efficiency gains translate to big cost savings. As technology costs come down and the pressure for faster fulfillment rises, more warehouses are incorporating “smart” features. In 2025 and beyond, trends like AI-driven warehouse management and robotics are becoming mainstream, making smart warehouses an exciting area of innovation in supply chain management.
6. Cold Storage Warehouses
Cold storage warehouses are specialized facilities designed to store temperature-sensitive and perishable goods in a chilled or frozen environment. These warehouses play a critical role in supply chains for food, pharmaceuticals, chemicals, and other products that must be kept within specific temperature ranges to preserve quality and safety. For example, a cold storage warehouse is essential for safely storing fresh produce, frozen meat, dairy products, or vaccines before they are distributed to stores or hospitals.
Cold storage warehouses maintain different temperature zones depending on the needs of the products:
Refrigerated (cool) storage: Typically 2°C to 8°C (35°F to 46°F). This is used for products that need to be kept cool but not frozen, such as fruits, vegetables, dairy, and certain medicines. Often called chill rooms, these areas prevent spoilage while avoiding freezing the goods.
Frozen storage: Below 0°C (often around -18°C to -25°C, or -0.4°F to -13°F) for deep freeze storage. It is required for items like ice cream, frozen meat/seafood, and long-term storage of foods to inhibit bacterial growth.
Maintaining these environments requires specialized refrigeration equipment, insulated construction, and strict operational procedures. Workers often need protective clothing, and equipment like forklifts might be adapted for cold temps. Energy costs are significant, as cooling must be constant, and warehouses have to minimize temperature fluctuations (for instance, using air locks or fast-closing doors to reduce warm air entering). Many cold warehouses also have backup power systems to protect products during outages.
The importance of cold storage has grown with modern consumer demands. As people consume more frozen foods, fresh produce year-round, and temperature-sensitive pharmaceuticals, cold chain logistics becomes vital. A failure in cold storage can lead to spoiled food or compromised vaccines, so these warehouses have robust monitoring systems. They often include climate control technology and sensors that alert managers if temperatures drift outside the set range, ensuring product quality is maintained throughout storage.
From a business perspective, cold storage warehouses allow companies to extend the shelf life of products and reach markets far away. For example, seafood caught in one country can be frozen and stored, then shipped globally on demand. By preserving goods in optimal conditions, cold warehouses help avoid waste and maintain inventory for when and where it's needed. They are a key type of warehouse in food and pharmaceutical supply chain management, enabling global distribution of perishable items while meeting safety standards.
7. Climate-Controlled Warehouses
Climate-controlled warehouses are storage facilities that regulate not just temperature, but also other environmental factors like humidity and air quality. While similar to cold storage, climate-controlled warehouses may not always operate at near-freezing temperatures – instead, they maintain a stable environment tailored to the products’ needs. This could mean keeping the warehouse around, say, 20°C (68°F) with low humidity, if that’s what the stored goods require. The goal is to protect sensitive items that could be damaged by extreme temperatures, moisture, or fluctuations in climate.
Products commonly stored in climate-controlled warehouses include electronics, fine art, antiques, musical instruments, wine, cosmetics, and certain pharmaceutical or chemical products that are stable at room temperature but sensitive to humidity or dust. For example, a furniture retailer might use a climate-controlled warehouse to prevent wood products from warping or growing mold (by controlling humidity), or an electronics distributor might need it to avoid condensation and corrosion on components.
A climate-controlled warehouse system actively regulates the environment inside the facility involving HVAC systems capable of heating, cooling, dehumidifying or humidifying the air as needed. Unlike a basic warehouse that might just be ambient (unconditioned) space, climate-controlled warehouses have insulated walls and advanced thermostats and sensors throughout. They monitor conditions and adjust as necessary to stay within tight parameters. For instance, if humidity rises on a rainy day, dehumidifiers kick in to maintain a dry atmosphere.
It’s important to note that climate-controlled is broader than just cold storage. Cold storage (discussed above) keeps things refrigerated or frozen. Climate control could mean cool, but not freezing, or simply stable room temperature with low humidity. For example, certain pharmaceutical ingredients might need to be kept between 15-25°C with less than 50% humidity – cooler than a hot warehouse in summer, but not refrigerator-cold. Climate-controlled warehouses fill this need.
The benefit of climate-controlled warehousing is protecting product integrity. By avoiding exposure to heat, cold, or moisture extremes, businesses prevent damage like melting, warping, rusting, mildew, or spoilage. Climate-contrlled warehouse is the best option if you have large quantities of goods that must be protected over long periods under consistent conditions. There is a cost to the level of control – energy bills can be high, and maintaining HVAC systems is an added expense. However, for valuable or sensitive inventory, the cost is justified by the reduced risk of product loss. Many eCommerce sellers of specialty goods (e.g. electronics or luxury items) opt for climate-controlled storage to ensure customers receive products in perfect condition, no matter the weather or season.
8. Cross-Docking Warehouses
Cross-docking warehouses (or cross-dock facilities) are designed to transfer shipments directly from incoming trucks to outgoing trucks with little or no long-term storage in between. In a cross-docking operation, products arriving at the warehouse are quickly sorted and loaded onto outbound vehicles for distribution, rather than being put away on shelves for days or weeks. The term comes from the concept of goods moving “across the dock” from inbound to outbound. The approach is all about speed and efficiency in the supply chain.
A typical cross-docking warehouse has a layout with two main areas: an inbound dock side and an outbound dock side, often with a small staging area in between. When a truck arrives with goods (say, a shipment from a supplier), those goods might be immediately allocated to several outbound orders. Warehouse staff (or automated systems) quickly sort the items by destination. They might break down pallets and recombine products for different delivery routes. Within a short time – sometimes mere hours – the goods are moved to an outgoing truck headed to their next destination (e.g., retail stores or regional distribution centers). The goal is to minimize or eliminate storage time; ideally, the products never even get shelved.
Cross-docking is often used in retail and perishable goods supply chains. For example, a grocery chain might receive deliveries of fresh produce daily. Rather than storing that produce, the distribution center uses cross-docking: incoming pallets of mixed fruits are quickly resorted into outbound trucks headed to individual stores the same day. This way, the produce spends minimal time in a warehouse, preserving freshness and reducing refrigeration needs. Another example is consolidating less-than-truckload (LTL) shipments: a cross-dock facility can take multiple small shipments from different suppliers and merge them into full truckloads destined for the same region, achieving shipping efficiency.
The advantages of cross-docking include reduced inventory holding costs (since items aren’t sitting in storage) and faster order fulfillment. It also means less warehouse space is needed for storage, which can lower real estate costs. However, cross-docking needs tight coordination – shipments must arrive on schedule and orders must be pre-planned so that the quick transfer is possible. It works best for fast-moving supply chains with stable, high-volume demand or for products that are pre-allocated to destinations (so minimal decision-making is needed on the fly).
Not every business model fits cross-docking. If your inbound supply is unpredictable or you need to hold stock to buffer against demand changes, pure cross-docking might not be feasible. Many warehouses use a hybrid approach: some goods are cross-docked when possible, while others are stored conventionally. Nonetheless, cross-docking warehouses are a powerful model for lean, just-in-time distribution, cutting down the need for storage in the supply chain and getting products to customers faster.
9. Consolidation Warehouses
A consolidation warehouse (or consolidated warehouse) is a facility that combines small shipments from multiple suppliers into one larger shipment to the same destination. The idea is to gather products from different sources, hold them until there’s a full load, and then send a single, consolidated shipment that is more economical. It is essentially the opposite of break-bulk. While break-bulk facilities receive one big shipment and distribute it out in smaller batches, consolidation warehouses collect small batches and merge them into a bigger one.
For example, imagine three small manufacturers each need to ship a pallet of goods to a retailer in another city every week. Individually, each pallet might be too small to fill a truck, and sending three separate trucks (or LTL shipments) is inefficient and costly. Instead, a consolidation warehouse can receive all three pallets, combine them into one truckload, and ship them together to the retailer. The retailer gets one large delivery instead of three, and the total transportation cost is lower when shared. The process benefits businesses by optimizing transport and often reducing shipping rates per unit weight or volume.
Consolidation warehousing is common in freight logistics and is often provided by 3PL companies or freight forwarders. These warehouses typically serve a staging function: they receive incoming small shipments, sort and group them by destination or delivery date, and then dispatch the consolidated loads. The time goods spend in the warehouse is usually just until enough cargo accumulates to justify a full shipment. It’s a bit of a balancing act – you wait long enough to consolidate efficiently, but not so long that customers face delays. Many companies use consolidation for routes where daily full loads aren’t feasible, effectively pooling shipments with others headed the same way.
The benefits of using a consolidated warehouse include lower transportation costs (full truckloads are cheaper per unit than multiple partial loads) and potentially more consistent delivery schedules. It also reduces the number of deliveries a customer or distribution point has to handle. According to logistics guides, “a consolidation warehouse is a third-party facility where small shipments from different customers are combined into larger, more economical truckloads bound for the same destination.” The strategy is especially useful for companies with limited inventory or startups that cannot fill large shipments on their own. By teaming up with others via a consolidator, they achieve scale.
One consideration is that all products in a consolidated shipment must be going to the same general destination or along the same route. So, consolidation warehouses work best when there is geographic concentration of deliveries. If your orders are very spread out, consolidation may not help.
10. Cooperative Warehouses
Cooperative warehouses are storage facilities owned and operated by a group of businesses or organizations that share the costs and resources. In a cooperative warehouse model, multiple companies with similar warehousing needs come together to form a cooperative (co-op) and run a warehouse collectively. Each member typically has a stake in the warehouse and a say in how it’s managed. It is different from a public warehouse where a provider serves many clients for profit – in a cooperative, the clients themselves are the owners.
Cooperative warehouses is common in industries like agriculture, where producers (farmers, growers) might pool resources to store and distribute their products. For instance, a group of wineries in a region could jointly own a cooperative warehouse to store wine cases before distribution. By sharing a larger facility, they each get access to better storage conditions (like climate control for wine) at a lower individual cost than if they each built their own warehouse. Cost-efficiency is a primary driver: all members split expenses for space, labor, equipment, and utilities, which can lower overall warehousing costs for each participant. Essentially, cooperative warehousing enables economies of scale for smaller players.
Another aspect is shared services. In a co-op warehouse, members might also share warehouse staff and management, security systems, and perhaps even integrated inventory software. Because it’s collectively operated, a cooperative warehouse often has a democratic management structure – decisions on operations, improvements, or fee structures are made jointly by the member companies. It ensures the warehouse services align with the members' common interests, rather than profits going to a third party.
The advantages of cooperative warehouses include:
Lower cost per business: By splitting fixed costs (rent, utilities, forklifts, etc.), each member pays less than maintaining a separate facility increasing each member’s profit margins.
Networking and collaboration: Members often are in similar industries, so the co-op can foster a community. For example, farmers sharing a warehouse might also share transportation or market information.
Access to larger infrastructure: Small companies gain access to a bigger, possibly better equipped warehouse (with say, advanced inventory systems or climate control) than they could afford alone.
However, there are challenges. Flexibility can be limited – each member must cooperate on decisions, which might slow down changes or improvements. If one member’s needs change drastically (say, one business suddenly needs much more space), it may be hard to accommodate without agreement. Also, the warehouse services might be somewhat generalized; if a member needs highly customized processes, a cooperative setup might not be ideal. Lastly, entering a cooperative often requires a commitment or membership agreement, which is less flexible than simply renting space month-to-month in a public warehouse.
11. Fulfillment Centers
Fulfillment centers are a specialized type of warehouse focused on
order fulfillment for eCommerce and retail. A fulfillment center stores inventory for various sellers and handles the entire process of receiving orders,
picking and packing products, and shipping orders to end customers. Companies like Amazon popularized the fulfillment center concept with their vast network (Amazon FBA centers), but many third-party logistics providers and dedicated fulfillment companies operate such centers for eCommerce brands.
Unlike a traditional warehouse that might simply hold goods, a fulfillment center is all about fast and accurate processing of individual orders. When an online store makes a sale, the fulfillment center is where the item is pulled from stock, packed into a box with the appropriate invoice or marketing inserts, labeled, and shipped out – often within the same day. These centers are equipped to handle a high volume of daily orders and usually integrate with online storefronts and marketplaces via software. Essentially, a fulfillment center functions as an outsourced logistics arm for businesses, allowing sellers to store their merchandise and outsource the pick-pack-ship operations to specialists.
Key characteristics of fulfillment centers:
They handle
inventory storage but with a focus on
ready-to-ship stock. Space is optimized for picking efficiency (e.g., bins and shelves for individual SKUs rather than only pallets).
They provide
order management and processing: when orders drop in from the seller’s online shop, the center’s team or automation systems immediately queue them for fulfillment.
Shipping and carrier management is part of the service: fulfillment centers arrange outbound shipping, often benefiting from bulk shipping discounts due to the large volume of packages sent daily.
Many offer
additional services like handling returns (reverse logistics), kitting (combining items into sets), or even customer service support for tracking.
For eCommerce businesses, using a fulfillment center (either their own or via a 3PL) can drastically improve shipping speeds and scalability. Instead of the seller packing boxes in their garage, a professional fulfillment center can send hundreds of orders per day with high accuracy. It makes businesses focus on marketing and product development while the logistics experts handle the operational details.
Fulfillment centers are essentially a subset of distribution centers, but typically the term “fulfillment center” implies
direct-to-consumer order fulfillment (B2C), whereas “distribution center” might serve stores or bulk shipments (B2B) as well. Many 3PL providers run multi-client fulfillment centers where they handle orders for many brands under one roof – each brand’s inventory is managed separately in the system, but the facility and labor are shared.
SendFromChina, for instance, offers order fulfillment services out of its Shenzhen fulfillment center, helping international sellers store products in China and fulfill worldwide orders efficiently.
12. How to Choose the Right Warehouse for Your Business
With so many warehouse types available, how do you determine which is the best fit for your business? Choosing the right warehouse (or combination of warehouses) comes down to understanding your specific operational needs and strategic goals. Here are some key factors to consider when evaluating warehousing solutions:
Your Storage Needs and Product Type
What kind of goods are you storing, and do they have special requirements? If you deal in perishable or temperature-sensitive goods, a cold storage or climate-controlled warehouse is a must. If your products are high-value or sensitive, you may need extra security or controlled conditions. For large volumes of standard goods, a public or private warehouse might suffice, whereas seasonal inventory surges might point to using on-demand public warehousing.
Volume and Turnover Rate
How quickly do your products move? If you have a high turnover and need daily order processing, a distribution center or fulfillment center is likely appropriate. For slower-moving inventory or overflow stock, a simple storage warehouse could work. High-volume eCommerce operations benefit from the speed of fulfillment centers, whereas wholesalers with palletized shipments might focus on distribution warehouses or consolidation centers.
Geographical Location
Consider warehouse location relative to your suppliers and customers. Multiple regional warehouses (or a distributed warehousing model) can shorten delivery times in key markets. If your customers are global but you manufacture in one country, you might use a bonded warehouse near the port of entry, or a fulfillment center in the destination country for faster local shipping. Transportation costs and time are heavily influenced by where your warehouse is.
Cost and Investment
Evaluate your budget for warehousing. Can you afford to invest in a private warehouse, or is it more cost-effective to pay for a 3PL (public warehouse or fulfillment service)? Calculate the total cost of ownership (rent, labor, utilities, equipment, taxes) for private warehousing versus the fees for
outsourcing. Smaller businesses often find 3PL warehousing or cooperative warehouses more affordable until they scale up. Also, consider contract terms – do you need flexible month-to-month space (pointing to public warehouses or on-demand warehousing) or can you commit to longer terms?
Value-Added Services and Technology
Determine if you need your warehouse to perform services beyond basic storage. Do you require pick and pack operations, labeling, assembly, returns handling, or real-time inventory visibility? If so, a facility like a fulfillment center or a well-equipped distribution center is more suitable. For example, if you want to promise 1-2 day shipping and live inventory stock levels on your website, partnering with a tech-enabled fulfillment center with robust WMS integrations will be important. Similarly, if automation is crucial for efficiency, look into smart warehouse capabilities or providers that use advanced systems.
13. Conclusion
Warehousing is a foundational component of logistics and supply chain management, but it’s clear that there is no single type of warehouse that fits all purposes. We’ve covered 11 types of warehouses – from public and private warehouses to specialized centers like bonded warehouses, cold storage, smart warehouses, and fulfillment centers – each serving unique roles in the supply chain. Understanding these differences is crucial for eCommerce businesses and any company looking to optimize its logistics.
14. FAQs
Q: What is the difference between a warehouse and a distribution center?
A: A warehouse is primarily for storing goods, while a distribution center focuses on rapidly moving goods through for distribution. Warehouses tend to hold products for longer periods. Distribution centers provide storage plus order processing, packing, and shipping, with goods often turning over quickly.
Q: When should a company use a public warehouse instead of a private warehouse?
A: Public warehouses are ideal for businesses that want flexibility and lower upfront costs. If your company is small, growing, or has fluctuating storage needs, a public (3PL) warehouse lets you rent space as needed without investing in your own facility.
Q: What types of products need a climate-controlled or cold storage warehouse?
A: Perishable food items (like produce, dairy, frozen foods) and pharmaceuticals (vaccines, medicines) typically need cold storage warehouses to stay within safe temperature ranges. Products like electronics, antiques, wine, cosmetics, or wooden furniture might require a climate-controlled warehouse if they are sensitive to temperature extremes or humidity.
Q: How does cross-docking differ from traditional warehousing?
A: In traditional warehousing, products are stored until needed – which could be days, weeks, or months. In cross-docking, storage is minimal. Goods coming in are quickly sorted and transferred to outgoing shipments without being shelved for long.
Q: What is a fulfillment center and how is it related to warehousing?
A: A fulfillment center is a type of warehouse specifically set up to handle order fulfillment for online or retail orders. It stores products but also manages picking items, packing boxes, and shipping to customers. It’s essentially the back-end of an eCommerce operation. Fulfillment centers are related to warehousing in that they involve storage, but they are highly service-oriented and time-sensitive, ensuring customer orders are processed quickly.