Table of Contents
What Is Automated Order Fulfillment? A Complete Guide for 2025
Time: Jul 24,2025 Author: SFC Source: www.sendfromchina.com
In today’s fast-paced e‑commerce landscape, customers expect lightning-fast delivery, zero errors, and seamless tracking. It is where automated order fulfillment steps in—a game-changing approach that harnesses smart software, robotics, and real‑time data to transform the journey from “buy now” to “package delivered.” Instead of relying on manual processes fraught with delays and mistakes, businesses can deploy systems that automatically capture orders, validate inventory, handle picking and packing, and dispatch shipments—with minimal human intervention.But it’s not just about speed. Automation slashes human error, streamlines reverse logistics, and unlocks vital insights for smarter decision-making. From nimble startups to global retail giants, the shift toward automated order fulfillment is reshaping supply chains—delivering higher accuracy, lower costs, and happier customers.
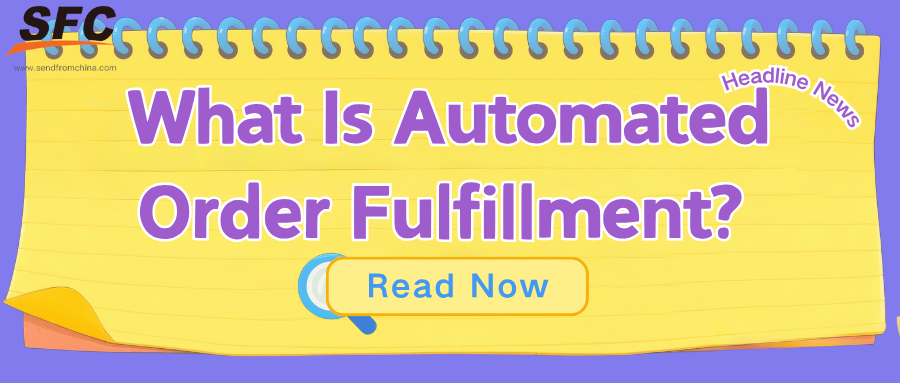
- What exactly automated order fulfillment involves
- Key benefits that matter most
- How the process operates end-to-end
- Steps to implement it effectively
- Tips for integrating it seamlessly within your supply chain
Let’s dive in.
1. What Is Automated Order Fulfillment?
Automated order fulfillment refers to the use of technology—like software, robotics, and AI—to handle every stage of getting a product into a customer’s hands. From the moment an order is placed, systems can pick, pack, and ship an item with minimal human involvement. It’s the central nervous system of modern logistics, replacing manual steps with seamless precision.In practice, these systems combine inventory management tools (WMS/OMS), storage-and-retrieval systems, barcode/RFID scanners, automatic conveyors, and packing robots. Together, they communicate in real-time—the order, available stock, warehouse layout, shipping carriers—ensuring each order moves efficiently through the fulfillment chain.
2. Benefits of Automated Order Fulfillment
Investing in automated order fulfillment delivers a powerful blend of speed, cost-efficiency, accuracy, and scalability—benefits that resonate across industries and business sizes. Here's how these advantages stack up: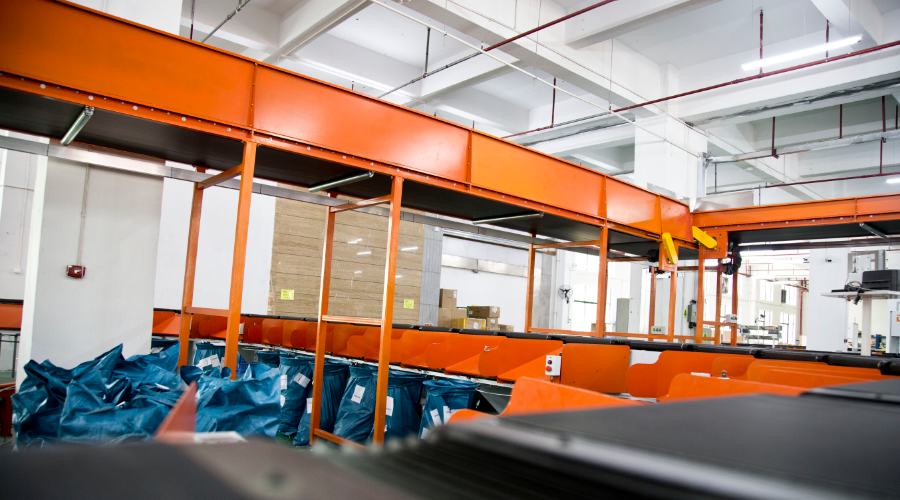
Faster Order Processing & Throughput
Automation slashes the cycle time from checkout to shipment. Systems instantly capture orders, verify payments and inventory, and trigger picking and packing workflows—often in seconds rather than minutes or hours. According to Omnidrop, this instantaneous workflow “reduces delays and improves customer satisfaction” by speeding delivery timelines.Case studies show operations handling 60–85% faster processing, with some achieving near real-time throughput even during peak demand.
Walmart reports its fully automated distribution centers manage twice the throughput with only half the staff—offering a fourfold efficiency gain.
Reduced Errors & Higher Accuracy
Automation mitigates manual entry mistakes, mis-picks, and mis-labels. Barcode scanners, RFID tech, and robotic picking enforce precision at every stage. A study from Next Matter highlights how automation systematically eliminates human error and boosts consistency across orders.With lower returns and fewer customer complaints, businesses preserve margin and trust. FulfillmentHubUSA confirms error reduction boosts customer satisfaction and loyalty.
Cost & Labor Savings
Automating tasks like label application, weighing, and sorting reduces reliance on manual labor. In one 3PL case, adding a checkweigher and label applicator on a conveyor line enabled single-shift handling of full volume—within budget.Meanwhile, robots like Amazon’s “Hercules” and “Robin” are projected to save the company $16 billion annually by 2032. Walmart's automation deployment also drove picking cost reductions and improved last-mile delivery density.
Scalable Operations
With automation, increasing order volumes—especially during holidays or flash sales—no longer demands proportional increases in staff. Systems flex with demand, handling surges without overtime, temp hires, or bottlenecks.Brightpick, a robotics provider, shows how plug-and-play robots allow rapid deployment, delivering faster ROI for growing operations.
Real-Time Inventory & Visibility
Automated systems update inventory levels in real time, across channels, reducing stockouts and overselling.Intelligent systems flag reorder points and can even trigger replenishment with suppliers—smoothing procurement and preventing out-of-stock disruptions.
Enhanced Customer Satisfaction
Faster, error-free fulfillment paired with real-time tracking boosts the overall shopping experience. Accurate delivery timelines reduce delays, and smart systems even handle reverse logistics more fluidly, improving customer retention.Data-Driven Insight & Optimization
Automated solutions provide dashboards tracking throughput, labor efficiency, error rates, and cost per order. This data empowers continuous refinement and strategic planning—balancing capacity, labor, and stock based on solid KPIs.Competitive Advantage & Future-Proofing
Brands in fashion, retail, and e‑commerce are adopting “smart warehouses” equipped with AI, robotics, RFID, and IoT. Industry giants like Harrods, LVMH, and Hugo Boss are investing heavily to enhance decision-making and sustainability.Smaller players can tap into these gains via modular automation from 3PL partners—boosting output by 10–50% without large CAPEX.
3. How Does Automated Order Fulfillment Work
Automated order fulfillment combines software, hardware, and smart workflows to streamline every stage—from when a customer places an order to the moment a package rolls onto a truck. Here's a detailed breakdown of each step: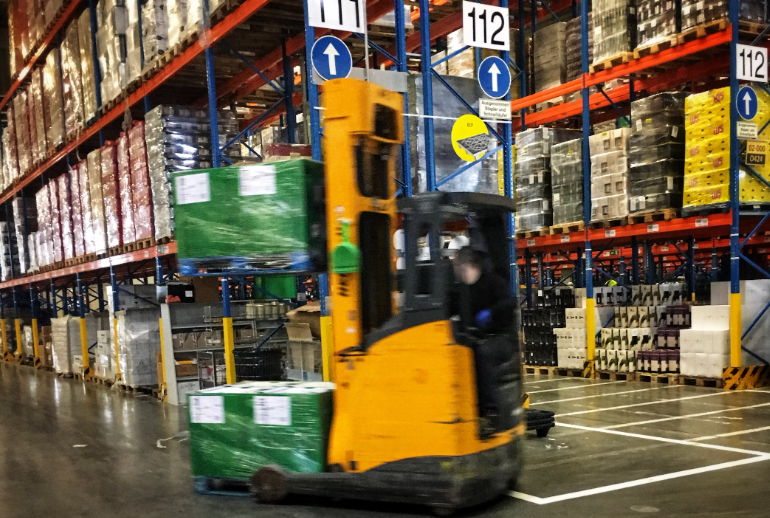
Order Capture & Validation
- Order Receipt: The moment a purchase is confirmed—whether via website, marketplace, or POS—the Order Management System (OMS) captures the order. It records SKUs, quantities, customer details, and payment status.- Validation: The OMS verifies payment, checks for fraud, and confirms stock availability. It integrates with Warehouse Management Systems and Enterprise Resource Planning (ERP) to ensure every detail is accurate before proceeding.
Inventory Allocation & Smart Routing
Once an order is validated, the system determines the optimal fulfillment strategy:- Dynamic warehouse selection, factoring in location, stock levels, and shipping costs. This reduces delivery times and minimizes expenses.
- Inventory reservation, where the WMS locks in the needed items, reducing the risk of overselling.
Orchestrated Picking
i. Warehouse Management System (WMS)WMS software drives the process, commanding resources and guiding order flow. It issues precise instructions—whether to a human worker or an automated system—about what, where, and how much to pick.
ii. Warehouse Execution System (WES) & WCS
- WES acts as a middle manager between WMS and equipment, directing and optimizing real-time tasks—receiving, sorting, picking, packing, and dispatching—based on current warehouse conditions.
- WCS interfaces directly with machinery (robotic arms, conveyors, sorters), ensuring smooth coordination and routing at decision points.
Automated Picking Technologies
- Automated Storage and Retrieval Systems (AS/RS)These automated racks and cranes retrieve items and bring them to picking stations, saving space and streamlining retrieval.
- Robotic Picking Arms, AGVs, and AMRs
- Robotic arms like Amazon’s Sparrow select and transfer individual items with precision.
- AGVs facilitate straightforward pallet or carton transport.
- AMRs map dynamic routes across the warehouse, transporting goods autonomously, guided by WMS/WES for optimal routing.
- Conveyor & Sortation Systems
Conveyors link various fulfillment stages, while sorters (like Amazon’s Pegasus and Xanthus) route items to correct packing zones or chutes.
Packing & Labeling
- Automated packing machines customize box size, weigh items, and dispense appropriate packing material, optimizing protection and lowering shipping costs.- Label printers and applicators generate shipping labels and route orders to their respective carriers or destinations seamlessly.
Dispatch & Shipping Integration
- Carrier assignment is automated based on predefined rules—cost, speed, or geography.- The TMS (or OMS) generates shipping manifests, batch labels, and dispatches packages to docks.
- Tracking information is sent automatically to customers, reducing support overhead.
Reverse Logistics (Returns)
Returns are no afterthought—automated systems scan returned items, assess condition, return stock, or route goods for inspection or restocking based on preset workflows.Real-Time Monitoring & Analytics
- IoT Sensors like RFID scanners, machine vision cameras, and IoT-enabled conveyor systems update inventory and order status in real time.- WES dashboards provide visibility into KPIs—cycle times, throughput, and backlog—enabling dynamic adjustments on the plant floor.
- AI-driven analytics forecast demand patterns and optimize resource deployment before bottlenecks even form.
4. How to Implement Automated Order Fulfillment
Implementing automation is a journey—starting with thoughtful planning and education, moving to pilot programs, and scaling up through continuous refinement. Below is a step-by-step roadmap: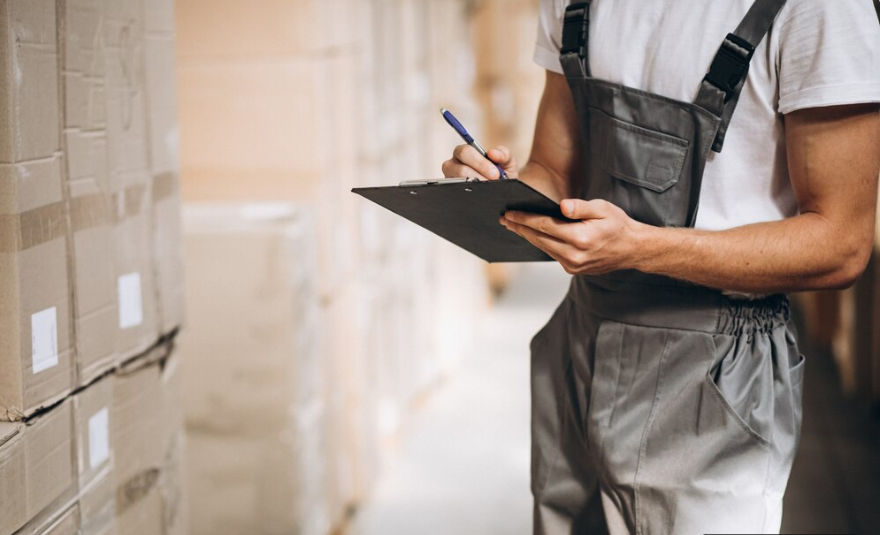
Step 1. Evaluate Current State & Set Clear Goals
- Map your workflows: Understand existing order-to-shipment processes. Document bottlenecks, redundancies, and manual handoffs. A mid-sized e-commerce provider reduced processing time by 30% and errors by 50% after revamping workflow maps.- Define KPIs: Identify targets like “cut pick-to-pack time by 40%” or “reduce mis-pick rate to under 1%.” These quantifiable goals guide strategy and ROI tracking.
Step 2. Determine Readiness & Select Target Areas
- Volume & SKU complexity: High-volume or high-SKU diversity environments benefit most from automation. AS/RS systems and robotics make sense only when scale is justified.- Infrastructure and tech stack: Assess your WMS/OMS, warehouse layout, and data systems. Automation thrives on integration, blending store platforms, ERP, order management, and execution layers like WES.
- Capital and ROI horizon: Cost of AS/RS might be steep, but deliver ROI in 2–5 years. Robotics and WMS upgrades may pay off in 6–24 months.
Step 3. Choose Technology & Partners
- Modular approach: Begin with less disruptive tools—pick‑to-light systems, weight‑based packing machines, or conveyor solutions—before scaling to full warehouse robots.- Vendor evaluation: Pick suppliers with strong integration track records. For JIT or omnichannel fulfillment, confirm seamless syncing with inventory & e-commerce platforms.
- Pilot under real workload: Test within a subset of SKUs or a warehouse zone. Measure throughput and error rates against KPIs, and adjust before enterprise rollout.
Step 4. Train Staff & Redefine Roles
- Shift human roles: As robots and systems take over manual work, staff transition into exception handling, systems monitoring, and analytics. Amazon reports employee roles shifting toward tech supervision with improved pay.- Change management: Provide robust training and support. Workers accustomed to manual tasks need time and tools to adapt to a technology-driven environment.
Step 5. Integrate Systems for Unified Workflow
- Connect WMS–WES–OMS–TMS: Automation depends on end-to-end coordination, ensuring data flows seamlessly from order capture through packing and dispatch.- Enable real-time inventory control: Integrate live inventory feeds to trigger replenishment, prevent stockouts, and maintain visibility across channels.
Step 6. Launch, Monitor & Optimize
- Pilot KPI assessment: Analyze throughput, error rates, labor-per-order, and cost savings. Sustainable success comes from improving these metrics in real use.- Iterate rapidly: Tweak workflows, machine speeds, buffer sizes, staffing levels, or software rules as bottlenecks shift. Automation only goes as far as continuous optimization.
- Scale systematically: Once pilots deliver results, expand automation to other zones, warehouses, product lines—and align supply chain partners where possible.
Step 7. Embed Sustainability & Long-Term Strategy
- Green initiatives: Incorporate sustainable best practices like optimized packaging sizes, reusable bins, and facility energy efficiency—trends that consumers and investors increasingly expect.- Stay future-ready: Explore JIT, cross-docking, and omnichannel fulfillment for greater velocity. An omnichannel strategy blends inventory across platforms from a single warehouse, enabling flexible workflows.
- Continuous improvement: Monitor new technologies—like collaborative mobile robots, AI-powered inventory planners, or voice-directed picking—for ongoing efficiency gains.
5. Integrating Automated Order Fulfillment with Your Supply Chain
To maximize value, automation must mesh seamlessly with your broader supply chain:- Omnichannel synergy: Unified inventory across e‑comm, retail, and wholesale enhances visibility and flexibility.
- Supplier linkages: Automated systems can trigger reorder points downstream, improving replenishment cycles and reducing stockouts.
- Warehouse network optimization: Fulfillment software can determine which distribution center should ship to reduce VT and cost.
- Returns coordination: Reverse logistics can be handled as efficiently as forward shipping—restocking, refurbishing, or discarding.
- Data flow to forecasting: Real-time visibility into picking speed, inventory aging, and order trends supports smarter procurement decisions and lowers carrying costs.
6. Conclusion
Automated order fulfillment isn’t just a tech upgrade—it’s a strategic shift. It accelerates speed, rockets accuracy, and reduces per-unit costs. With giants like Walmart and Amazon setting the pace, automation is no longer a novelty; it’s essential for competitiveness in e‑commerce and retail. By carefully assessing needs, piloting solutions, and integrating across supply chains, businesses can unlock efficiency, scalability, and happier customers.7. FAQs
1. Is automation only for big companies?
Not at all. Scalable automation—from smart shelving to partial robotics—is available for mid‑sized businesses too. The key is starting with a pilot.2. Does automation replace workers?
Mostly, it redefines jobs. Labor shifts from manual tasks to system oversight, maintenance, and data management. Often, head counts stay stable even as throughput increases.3. What tech is needed for automation?
Core components include WMS/OMS software, conveyors, AS/RS, barcode/RFID scanning, packing machines, and robots.4. How long until ROI from automation?
Depending on scope and scale, many businesses see returns within 12–24 months, driven by cost savings, fewer errors, better throughput, and improved customer loyalty.5. Can automation handle returns?
Yes—modern systems include reverse logistics. Returns are scanned, classified, restocked, or routed automatically, keeping inventory accurate and costs down.
Copyright statement: The copyright of this article belongs to the original author. Please indicate the source for reprinting.
Previous Post
Optimizing Ecommerce Logistics with Strategic Supply Chain Planning
Next Post
Inventory Backlog Explained: Definition, Formulas, and Prevention Strategies
TAGS
Hot Research
Get a Custom China Fulfillment Solution with FREE Storage for 60 Days
Want to know about our services, fees or receive a custom quote?
Please fill out the form on the right and we will get back to you within a business day.
The more information you provide, the better our initial response
will be.