Table of Contents
Top 10 Essential Functions of a Warehouse: A Comprehensive Guide
Time: Apr 28,2025 Author: SFC Source: www.sendfromchina.com
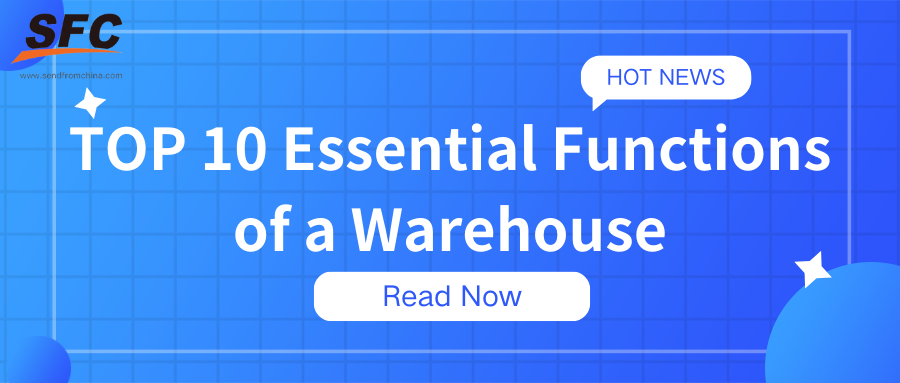
1. Understanding Warehouse Functions?
2. 10 Common Warehouse Functions
Function 1: Receiving
Key Steps in the Receiving Process
Pre-Receiving Preparation: Before goods arrive, it's essential to prepare the receiving area by ensuring adequate space, necessary equipment, and updated documentation. Coordinating with suppliers about delivery schedules and requirements can streamline the process.Unloading: Upon arrival, goods are unloaded from transportation vehicles. Careful handling during this stage prevents damage and facilitates easier inspection.
Inspection and Verification: Each shipment is inspected for quantity and quality, ensuring it matches the purchase order and is free from damage. Discrepancies are documented and addressed promptly.
Documentation: Accurate records are maintained for each received shipment, including details like item descriptions, quantities, and any noted damages. This information is vital for inventory tracking and financial reconciliation.
Labeling and Barcoding: Products are labeled or barcoded to facilitate easy identification and tracking within the warehouse management system (WMS).
Putaway Preparation: After verification, goods are prepared for storage by determining appropriate storage locations based on factors like item type, size, and demand frequency.
Best Practices for Efficient Receiving
Implement Standard Operating Procedures (SOPs): Establishing clear SOPs ensures consistency and reduces errors during the receiving process.Utilize Technology: Employing tools like barcode scanners and WMS can enhance accuracy and efficiency. These technologies assist in real-time data entry and inventory updates.
Train Staff Regularly: Continuous training ensures that staff are knowledgeable about procedures, safety protocols, and the use of technology.
Maintain a Clean and Organized Receiving Area: An orderly workspace minimizes the risk of errors and accidents, facilitating smoother operations.
Monitor and Evaluate Performance: Regularly assessing the receiving process helps identify areas for improvement and implement necessary changes.
Function 2: Quality Check
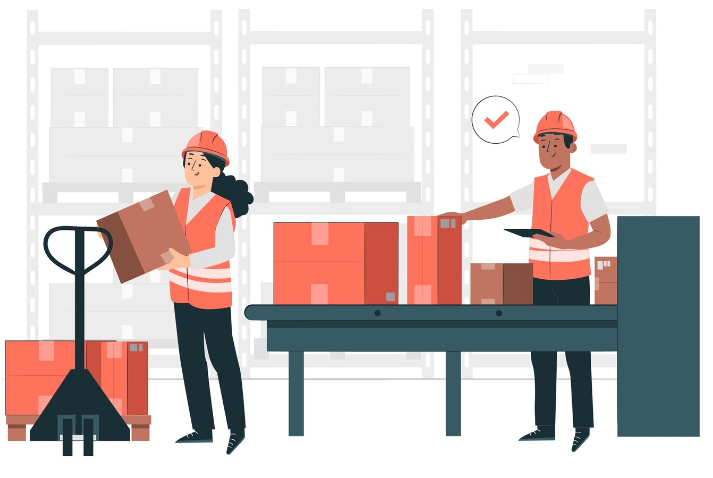
Key Components of Warehouse Quality Control
Inspection Procedures: Regular inspections are conducted at various stages—receiving, storage, picking, and shipping—to identify and rectify defects or discrepancies.Standardized Checklists: Utilizing checklists ensures consistency in inspections, covering aspects like packaging integrity, labeling accuracy, and product condition.
Sampling Techniques: Implementing sampling methods, such as random or stratified sampling, helps in assessing product quality without inspecting every item.
Documentation and Reporting: Maintaining detailed records of inspections, non-conformities, and corrective actions facilitates continuous improvement and compliance tracking.
Integration with Warehouse Management Systems: Leveraging WMS allows for real-time tracking of quality metrics, automated alerts for deviations, and streamlined workflows.
Function 3: Putaway
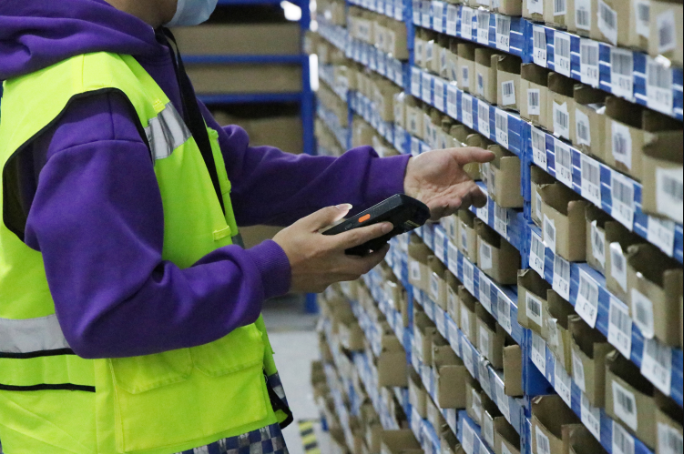
Types of Putaway Strategies
Fixed Location Putaway: Each SKU is assigned a specific location. This method simplifies retrieval but may lead to inefficient space utilization if demand varies.Dynamic Putaway: Goods are stored in any available space, optimizing storage density. However, it requires a robust Warehouse Management System to track item locations accurately.
Directed Putaway: The WMS suggests optimal storage locations based on factors like item size, weight, and demand frequency, balancing efficiency and organization.
Zone-Based Putaway: The warehouse is divided into zones, and items are stored in designated areas based on their characteristics or demand patterns. This method reduces travel time during picking.
ABC Analysis-Based Putaway: Items are categorized into three groups based on their value and demand. High-value, high-demand items (A) are stored in easily accessible locations, while lower-value items (B and C) are placed in less accessible areas.
Best Practices for Effective Putaway
Utilize Technology: Implementing barcode scanners and RFID systems enhances accuracy and speed in tracking item movements.Optimize Warehouse Layout: Designing the warehouse to minimize travel distances and grouping similar items can significantly improve putaway efficiency.
Train Staff: Regular training ensures that warehouse personnel are proficient in putaway procedures and aware of safety protocols.
Monitor and Analyze Data: Regularly reviewing putaway performance metrics helps in identifying bottlenecks and areas for improvement.
Function 4: Storage
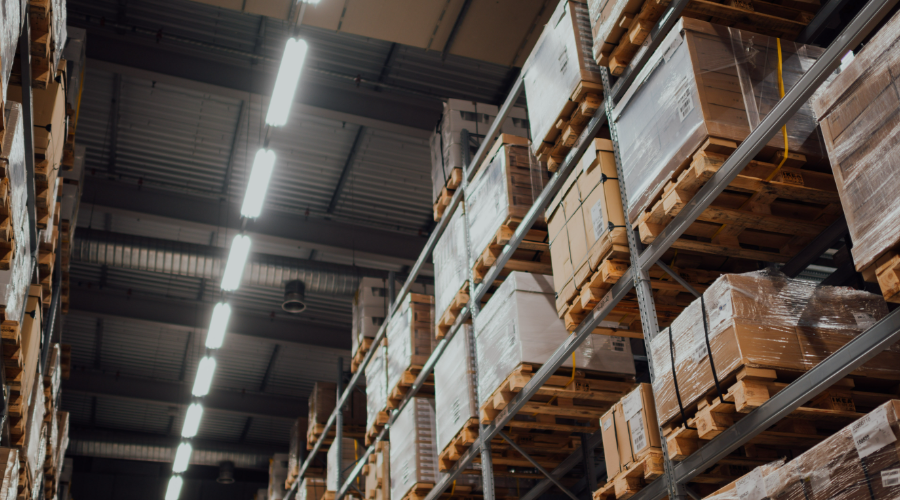
Types of Warehouse Storage Systems
Static Shelving: Fixed shelving units suitable for storing smaller items that require manual picking.
Mobile Shelving: Mounted on tracks, these shelves can be moved to create access aisles, optimizing space usage.
Mezzanine Flooring: An intermediate floor built within the warehouse to increase storage capacity without expanding the building footprint.
Cantilever Racking: Designed for storing long, bulky items like pipes and lumber, with arms extending from a central column.
Best Practices for Efficient Storage
Implement ABC Analysis: Categorize inventory based on demand, with 'A' items being high-demand products stored in easily accessible locations, and 'C' items being low-demand products stored further away.
Optimize Aisle Widths: Design aisles to accommodate equipment while minimizing wasted space, balancing accessibility with storage density.
Regularly Review Inventory Levels: Conduct periodic audits to ensure that storage space is used effectively and to identify obsolete or slow-moving stock.
Leverage Technology: Use Warehouse Management Systems to track inventory locations, manage stock levels, and optimize storage assignments.
Function 5: Inventory Management
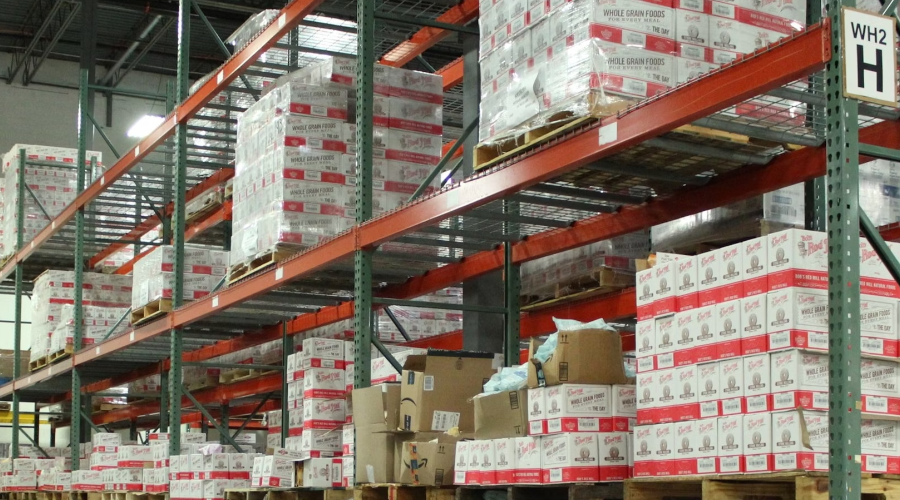
Key Components of Inventory Management
Stock Tracking: Maintaining accurate records of inventory levels, locations, and movements is essential. This involves real-time monitoring to ensure data accuracy and facilitate decision-making.Demand Forecasting: Analyzing historical sales data and market trends helps predict future product demand, enabling proactive inventory planning and procurement.
Reorder Point Calculation: Determining the optimal inventory level at which new stock should be ordered prevents stockouts and maintains service levels.
Safety Stock Management: Maintaining a buffer stock to account for demand variability and supply chain disruptions ensures continuity in operations.
Inventory Turnover Analysis: Assessing how frequently inventory is sold and replaced over a period helps identify slow-moving items and optimize stock levels.
Best Practices for Effective Inventory Management
Implementing Inventory Management Systems (IMS): Utilizing software solutions for real-time tracking, automated alerts, and data analytics enhances accuracy and efficiency.Regular Audits and Cycle Counting: Conducting periodic physical counts of inventory helps identify discrepancies and maintain data integrity.
ABC Analysis: Categorizing inventory into three classes (A: high-value, B: moderate-value, C: low-value) allows for prioritized management and resource allocation.
Just-In-Time (JIT) Inventory: Aligning inventory orders closely with production schedules reduces holding costs and minimizes waste.
Vendor-Managed Inventory (VMI): Collaborating with suppliers to manage inventory levels can streamline replenishment processes and improve supply chain integration.
Benefits of Robust Inventory Management
Cost Reduction: Optimizing inventory levels minimizes storage costs, reduces capital tied up in stock, and decreases obsolescence.Improved Customer Satisfaction: Ensuring product availability enhances service levels and customer loyalty.
Enhanced Operational Efficiency: Streamlined inventory processes contribute to faster order fulfillment and reduced lead times.
Data-Driven Decision Making: Access to accurate inventory data supports strategic planning and responsive supply chain management.
Function 6: Order Picking
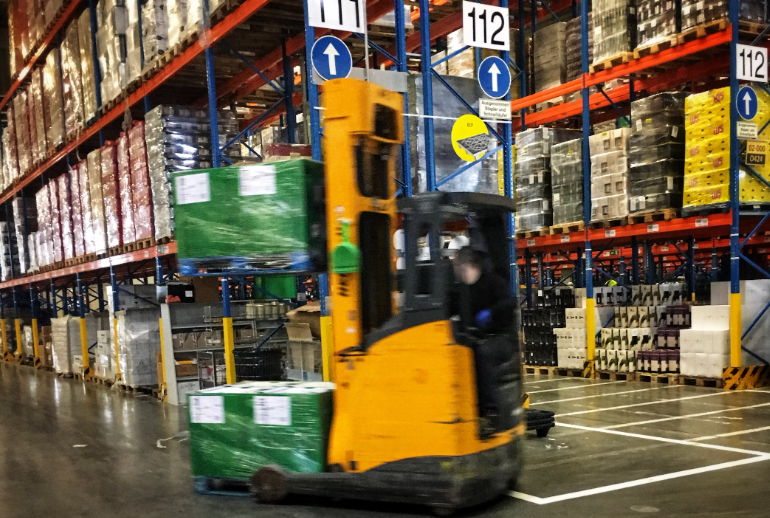
Common Order Picking Methods
Batch Picking: A picker collects items for multiple orders simultaneously, reducing travel time. However, it requires sorting items into individual orders after picking.
Zone Picking: The warehouse is divided into zones, and pickers are assigned to specific zones. Orders are passed from one zone to another until complete. This method reduces picker travel but requires coordination between zones.
Wave Picking: Combines aspects of batch and zone picking. Orders are grouped into waves based on factors like shipping schedules, and pickers retrieve items accordingly.
Cluster Picking: A picker retrieves items for multiple orders simultaneously, placing them into separate containers (clusters). This method increases efficiency but requires careful organization to prevent errors.
Best Practices for Efficient Order Picking
Implement Technology: Utilize Warehouse Management Systems, barcode scanners, and pick-to-light or voice-picking systems to guide pickers and reduce errors.
Regular Training: Provide ongoing training for pickers to ensure they are familiar with procedures and technologies.
Monitor Performance Metrics: Track key performance indicators (KPIs) such as pick rate, accuracy, and order cycle time to identify areas for improvement.
Maintain Clean and Organized Picking Areas: A tidy workspace minimizes errors and enhances safety.
Function 7: Packing
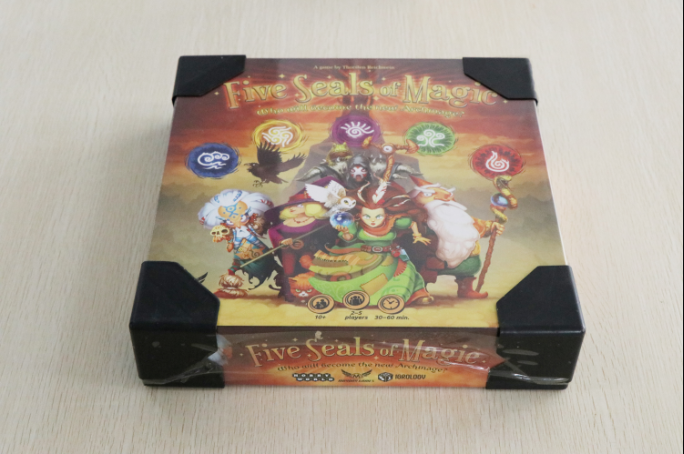
Key Elements of the Packing Process
Verification and Quality Control Before packing, items are verified against the order details to ensure accuracy. This step helps prevent errors such as incorrect items or quantities being shipped. Quality control checks are also performed to identify any damaged or defective products before they reach the customer.Selection of Appropriate Packaging Materials Choosing the right packaging materials is essential to protect products during transit. This includes selecting suitable box sizes, cushioning materials like bubble wrap or foam, and sealing methods to prevent tampering or damage.
Efficient Use of Space and Materials Optimizing the use of packaging materials and space within boxes can reduce shipping costs and environmental impact. Using appropriately sized boxes minimizes the need for excessive filler materials and allows for more efficient stacking during transportation.
Labeling and Documentation Accurate labeling is crucial for ensuring that packages are delivered to the correct destination including affixing shipping labels with barcodes, handling instructions, and any necessary customs documentation for international shipments.
Integration with Warehouse Management Systems Utilizing a WMS can streamline the packing process by providing real-time data on inventory levels, order details, and shipping requirements. This integration helps coordinate packing activities with other warehouse functions, improving overall efficiency.
Best Practices for Efficient Packing
Implement Standard Operating Procedures (SOPs): Establishing clear SOPs for packing ensures consistency and reduces errors across different shifts and personnel.Train Staff Regularly: Ongoing training programs keep staff updated on the latest packing techniques, safety protocols, and use of equipment.
Utilize Technology: Incorporating tools such as barcode scanners, automated packing machines, and conveyor systems can enhance speed and accuracy.
Monitor Performance Metrics: Tracking key performance indicators (KPIs) like packing speed, error rates, and material usage helps identify areas for improvement.
Maintain a Clean and Organized Packing Area: An orderly workspace reduces the risk of errors and accidents, contributing to a safer and more efficient packing process.
Function 8: Shipping
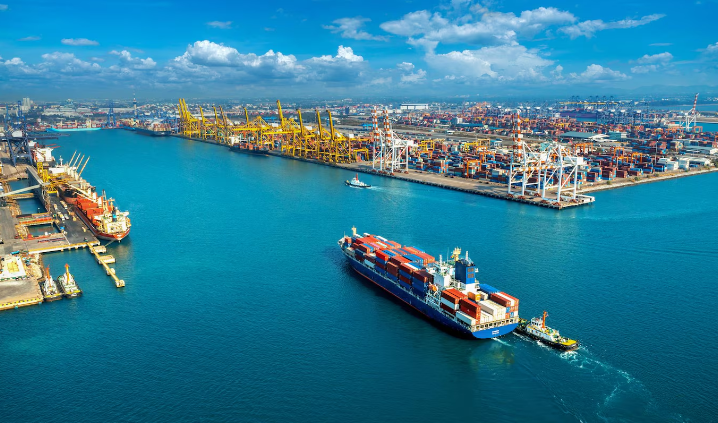
Key Steps in the Shipping Process
Order Verification Before dispatch, each order undergoes a verification process to confirm that the correct items are packed, quantities are accurate, and shipping details match the customer's order.Weighing and Dimensioning Accurate measurement of package weight and dimensions is essential for determining shipping costs and ensuring compliance with carrier requirements.
Labeling Shipping labels are generated and affixed to packages, containing vital information such as destination address, tracking number, and handling instructions.
Carrier Selection and Scheduling Based on factors like delivery speed, cost, and destination, the appropriate carrier is selected, and pickup is scheduled to ensure timely delivery.
Loading and Dispatch Packages are organized and loaded onto transportation vehicles in a manner that optimizes space and ensures the safety of goods during transit.
Documentation and Tracking Shipping documentation, including invoices and bills of lading, is prepared. Tracking information is updated in the system to provide real-time visibility to both the warehouse and the customer.
Best Practices for Efficient Shipping
Implement Warehouse Management Systems: Utilizing WMS can streamline the shipping process by automating tasks such as label generation, carrier selection, and tracking updates.Optimize Warehouse Layout: Designing the warehouse to facilitate smooth movement from packing stations to loading docks can reduce handling time and errors.
Regular Training: Ensuring that staff are well-trained in shipping procedures and safety protocols can enhance efficiency and reduce the risk of accidents.
Monitor Key Performance Indicators: Tracking metrics such as order accuracy, shipping time, and cost per shipment can help identify areas for improvement.
Maintain Strong Carrier Relationships: Collaborating closely with carriers can lead to better rates, improved service levels, and more reliable delivery schedules.
Function 9: Returns Processing
Key Steps in the Returns Process
Return Initiation and Authorization The process begins when a customer initiates a return, often through an online portal or customer service. A Return Merchandise Authorization (RMA) is generated, providing a unique identifier for tracking the return throughout the process.Receiving Returned Goods Upon arrival at the warehouse, returned items are directed to a designated returns area. This separation from regular inventory prevents cross-contamination and ensures focused processing.
Inspection and Sorting Each item is inspected to assess its condition and determine the appropriate disposition: restock, refurbish, recycle, or dispose. This step is crucial for maintaining inventory accuracy and quality control.
Refurbishment: Products requiring minor repairs or repackaging are processed accordingly.
Recycling/Disposal: Damaged or non-resalable items are recycled or disposed of following environmental guidelines.
Customer Refund or Replacement After processing, customers are issued refunds, replacements, or store credits as per the company's return policy. Timely resolution is vital for customer satisfaction.
Best Practices for Efficient Returns Processing
Implement a Clear Returns Policy: A transparent and customer-friendly returns policy sets expectations and streamlines the process.Leverage Technology: Utilize Warehouse Management Systems to track returns, manage inventory updates, and generate reports for continuous improvement.
Designate a Dedicated Returns Area: Having a specific zone for handling returns prevents disruption to regular operations and allows for specialized processing.
Train Staff Regularly: Ensure that employees are well-versed in returns procedures, including inspection standards and safety protocols.
Analyze Returns Data: Regularly review return reasons and patterns to identify product issues, improve quality, and reduce future returns.
Function 10: Cross-Docking
How Cross-Docking Works
Sorting: Products are sorted based on their destinations.
Transferring: Sorted products are moved directly to outbound docks.
Shipping: Products are loaded onto outbound trucks for delivery.
Types of Cross-Docking
Pre-Distribution Cross-Docking: In this model, the destination of goods is known before they arrive at the cross-docking facility. Products are pre-packaged and labeled for specific destinations, allowing for immediate transfer upon arrival.Post-Distribution Cross-Docking: Here, the destination of goods is determined after they arrive at the facility. Products are sorted and consolidated based on current demand and shipping schedules before being dispatched.
Consolidation Cross-Docking: This involves combining shipments from multiple suppliers into a single shipment for delivery to a customer. It reduces transportation costs and improves efficiency.
Deconsolidation Cross-Docking: Large shipments are broken down into smaller loads for distribution to multiple destinations. It is common in retail distribution where large quantities are received and then distributed to various stores.
Benefits of Cross-Docking
Reduced Storage Costs: By minimizing the need for storage, warehouses can save on space and associated costs.Improved Delivery Times: Direct transfer of goods speeds up the delivery process, enhancing customer satisfaction.
Lower Handling Costs: Less handling reduces labor costs and the risk of product damage.
Inventory Optimization: Cross-docking supports just-in-time inventory practices, reducing the need for large inventory holdings.
Challenges and Considerations
Coordination: Effective cross-docking requires precise coordination between suppliers, transportation providers, and warehouse staff.Technology: Advanced Warehouse Management Systems are essential for tracking and managing the flow of goods.
Facility Design: Warehouses must be designed to facilitate the quick movement of goods from inbound to outbound docks.
3. Conclusion
4. FAQs
What is the primary function of a warehouse?
The primary function is to store goods securely until they are needed for distribution or sale.How does inventory management benefit a warehouse?
It ensures optimal stock levels, reduces holding costs, and improves order fulfillment accuracy.What is cross-docking in warehousing?
Cross-docking involves transferring products directly from inbound to outbound transport, minimizing storage time.Why is quality control important in a warehouse?
It ensures that only products meeting quality standards are shipped, reducing returns and enhancing customer satisfaction.How do warehouses handle returned goods?
Returned items are inspected, and based on their condition, they are restocked, repaired, or disposed of appropriately.
Copyright statement: The copyright of this article belongs to the original author. Please indicate the source for reprinting.
Previous Post
Warehouse Mapping: the Key to Efficient Ecommerce Fulfillment
Next Post
What Is Supply Chain Forecasting? Types, Methods & Key Features Explained
TAGS
Hot Research
Recent News
Get a Custom China Fulfillment Solution with FREE Storage for 60 Days
Want to know about our services, fees or receive a custom quote?
Please fill out the form on the right and we will get back to you within a business day.
The more information you provide, the better our initial response
will be.