Table of Contents
Cloud WMS Explained: What Is Cloud‑Based Warehouse Management Software?
Time: Jul 15,2025 Author: SFC Source: www.sendfromchina.com
Are you struggling with outdated warehouse systems that can’t keep pace with today’s fast-moving supply chains? Imagine managing inventory in real time, executing orders across borders with ease, and scaling operations without costly hardware upgrades. That’s exactly what cloud warehouse management software brings to the table.In this post, you’ll learn what a cloud-based Warehouse Management System (WMS) is, why it’s rapidly overtaking legacy on-premise systems, and how it delivers key benefits—from cost savings and security to seamless integrations and analytics. We’ll guide you through the core features to look for, show you step-by-step how to implement a cloud WMS, and explain how SendFromChina’s cloud platform revolutionizes 3PL fulfillment.
By the end, you’ll have a clear, actionable roadmap for transforming your warehouse into a modern, scalable hub—and the confidence to choose the right solution for your business.
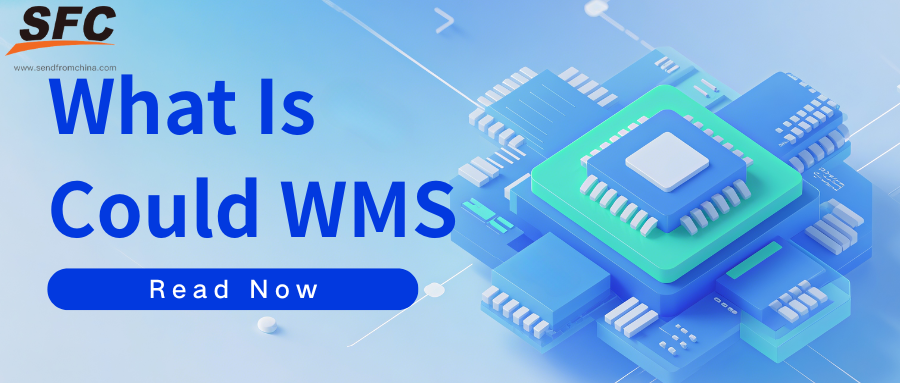
1. What Is a Cloud WMS
A cloud-based Warehouse Management System (cloud WMS) is a software platform designed to manage, control, and optimize a warehouse’s daily operations—hosted remotely and accessed via the internet. Unlike traditional, on‑premise systems that require in‑house servers and hefty IT support, cloud WMS runs on external servers, leveraging modern cloud infrastructure.These systems give businesses:
- Remote access: operators and managers can monitor inbound, outbound, picking, packing, and shipping in real‑time from any internet-connected device.
- Centralized data repository: all warehouse locations feed live data into a single dashboard, eliminating decision delays due to siloed systems.
- Subscription-based pricing, avoiding large upfront investments in hardware and licensing.
At its core, a cloud WMS transforms warehouse operations into a connected, data-driven service—one that scales with your business without the burden of physical infrastructure.
2. Advantages of a Cloud Warehouse Management System
Making the shift to a cloud-based WMS unlocks far-reaching benefits, reshaping how warehouses operate from the ground up. Let’s explore these, supported by recent data and diverse perspectives.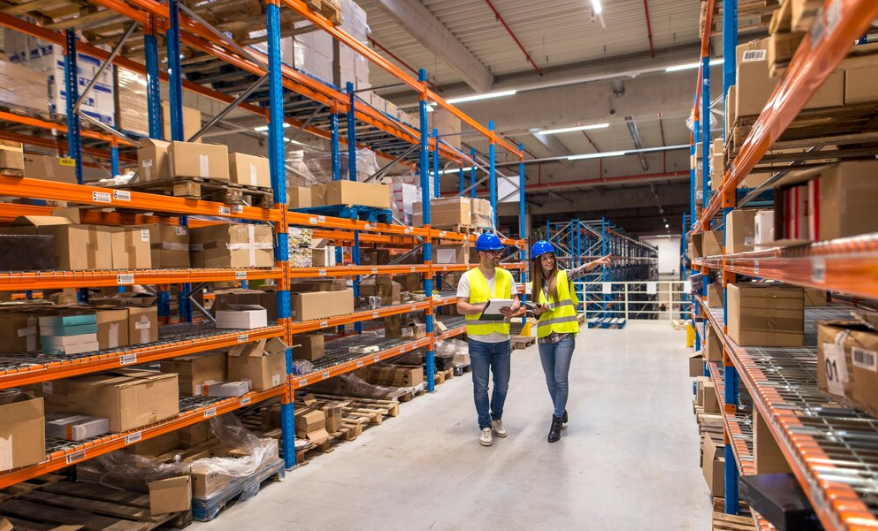
Scalability & Flexibility
Cloud WMS can adjust storage and computing resources dynamically. Whether coping with seasonal peaks or expanding into new regions, it scales effortlessly—no new servers needed. VMware reports businesses cut infrastructure costs by about 41% by migrating to the cloud.Cost Efficiency
The pay-as-you-go model shifts costs from capital expenditures to operational ones. No hardware to buy, no software licenses, and the provider manages updates and maintenance.Real-Time Visibility & Control
Live data means accurate inventory levels, faster order processing, and fewer errors. All key warehouse KPIs become accessible from anywhere.Seamless Integration
Cloud WMS platforms readily integrate with ERP, CRM, TMS, e‑commerce platforms, barcode scanners, RFID, and IoT systems—eliminating manual entries and streamlining order-to-ship workflows.Enhanced Security & Disaster Recovery
Providers employ robust cloud-security protocols—data encryption, intrusion detection, regular backups, and disaster recovery—often representing a level of protection businesses can’t afford in-house.Operational Efficiency & Automation
Typical improvements include automated receiving and put-away, picking route optimization, and guided workflows. It leads to faster processing, fewer errors, less labor, and improved accuracy.Advanced Analytics & Reporting
Automated dashboards highlight trends like inventory velocity and picking efficiency in real time. The level of insight drives smarter decisions and faster cycle counts.Quick Deployment & Updates
Without the need to configure servers, cloud WMS can be live in weeks, not months—and providers continuously update the system for you.3. Core Features of Cloud WMS
A high-quality cloud-based WMS goes well beyond basic inventory tracking. It's a centralized powerhouse with intelligent tools that coordinate every aspect of warehouse operations. Here's a refined breakdown of the core capabilities that modern facilities rely on: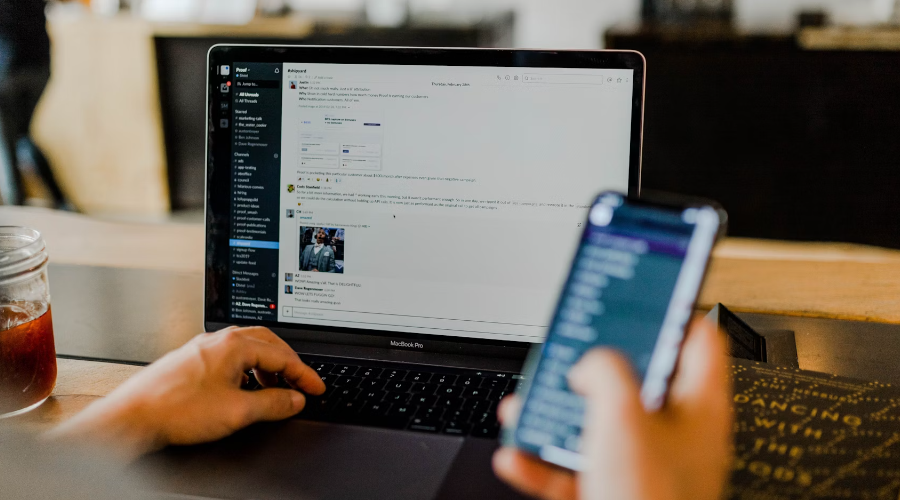
Real-Time Inventory Control & Visibility
Live stock levels & location awareness: Every movement—receiving, transfers, picking, shipping—is logged instantly, ensuring you always know exactly what’s on hand and where it is.Multi-warehouse support: Manage and redistribute inventory across multiple facilities from a single dashboard—critical for businesses operating globally or via multiple sites.
Order Management & Fulfillment
Streamlined order workflows: The system handles everything—order validation, wave or batch picking, intelligent packing, and shipping label generation—while minimizing delays and picking mistakes.Complex order handling: Ideal for businesses using kitting, bundle packing, or partial shipments—ensuring the right configuration reaches the right destination efficiently.
Mobile Capabilities & Scanning Integration
Barcode & RFID support: Warehouse staff can scan items and locations directly via mobile or wearable devices, connecting physical actions to real-time digital updates.Guided workflows: Scanning triggers visual or audio guidance, steering pickers through zones efficiently and drastically reducing errors.
Automation & Workflow Optimization
Automated task generation: The system intelligently assigns picking, packing, and put-away tasks based on priority and worker availability, accelerating operations.Slotting & layout optimization: AI-driven algorithms suggest storage locations based on sales velocity, package size, and seasonal trends—optimizing both space and picking speed.
Seamless Integration Ecosystem
Plug-and-play API connections: Easily links with ERP, CRM, transportation systems, e‑commerce platforms, and third-party logistics(3pl) partners, enabling smooth, automated data flows.Unified data ecosystem: Integration ensures changes in inventory or orders propagate automatically, reducing manual errors and data silos.
Reporting, Analytics & Intelligence
Interactive dashboards: Track KPIs like order accuracy, labor productivity, and pick/pack rates; drill down into data to surface bottlenecks and inefficiencies.Advanced analytics: Pre-built modules support ABC analysis, cycle-count planning, and forecasting—leveraging historical data to drive smarter warehouse strategies.
Security, Compliance & Data Integrity
Enterprise-level security: Encryption, role-based access, audit logs, and compliance certifications form a tight security fabric.Resilient backups: Frequent snapshots and cross-regional data backup ensure rapid recovery in case of outages or disruptions.
Labor & Resource Management
Task orchestration: Assign work based on real-time metrics and skill sets, while tracking productivity, idle time, and overutilization.Performance tracking: Generate labor reports to monitor trends in efficiency and training needs.
Rapid Deployment & Configurability
Fast implementation: With no physical infrastructure needed, cloud WMS can be piloted and deployed within weeks.Configurable workflows: Easily adapt processes—task prioritization, packing rules, or user interfaces—to match unique warehouse operations.
Future-Ready Features
AI/ML-enabled optimizations: Many systems are embedding machine learning for smarter forecasting, routing, and labor planning.IoT and real-time connectivity: Live feed from devices—such as environmental monitors or automated guided vehicles (AGVs)—integrates directly with cloud WMS for proactive adjustments.
4. How to Implement Cloud Warehouse Management Systems
Transitioning to a cloud WMS is more than just switching software—it’s a strategic transformation that involves strategy, coordination, and continuous improvement. Below is a robust, multi-phase roadmap drawing from expert frameworks and leading industry practices.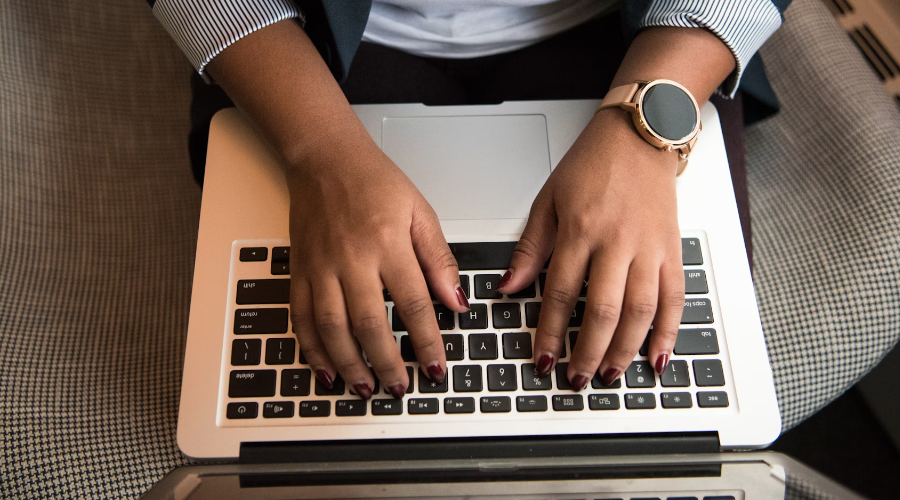
Step 1: Define Goals & Assemble Project Team
Clarify your objectives—Do you need faster picking, better inventory accuracy, multi-warehouse control, or improved labor management? Define measurable KPIs from day one (e.g. “reduce picking time by 25% in quarter one”).Identify and engage stakeholders from operations, IT, warehouse staff, 3PL partners, and finance. Their buy-in ensures alignment on requirements, timelines, and change management.
Form your WMS implementation team, led by a strong project manager and supported by internal champions and vendor contacts. Make communication flow smoothly between all parties.
Step 2: Assess Current Warehouse Processes
Conduct a detailed audit of current workflows—receiving, put-away, picking, packing, shipping, and returns. Capture layout, SKU profiles, inventory accuracy, and major pain points.Map out physical zones (bins, racks, packing, staging), and ensure hardware—scanners, conveyors, scales—is ready. Label bins and install barcodes or RFID tags in advance.
Clean up data—correct inconsistencies in SKUs, bin assignments, and inventory records to ensure smooth migration.
Step 3: Vendor Selection & Strategy
Evaluate potential cloud WMS providers with an eye on functionality, integration (API readiness), cost structure, and scalability.Conduct vendor demos and trials with scenarios specific to your operation (e.g., batch picking, returns processing).
Request client references and case studies, particularly in your industry or scale.
Step 4: Configuration & Integration
Kick-off configuration with the vendor—set up your cloud instance, customize workflows, thresholds, task priorities, and alerts.Integrate with core systems—ERP, e-commerce platforms, TMS, shipping/carriers. Map data flows like order imports, inventory syncs, shipping notifications, and billing.
Hardware integration—connect scanners, RFID readers, conveyors, scales, and packing equipment so physical actions update the system in real time.
Step 5: Testing & Pilot Phase
Pilot with a controlled SKU set or zone to test routing, inventory accuracy, pick performance, and system logging.Use phased or parallel adoption—run the cloud WMS alongside your legacy system to reduce risk.
Track results using KPIs and gather staff feedback to refine system logic, user prompts, and integration flows.
Step 6: Training & Change Management
Roll out hands-on training—tailored to user roles (pickers, packers, managers), focusing on scanning, workflows, and exception resolution.Leverage your implementation team as peer trainers—this builds internal expertise and strengthens adoption.
Manage change proactively—communicate benefits, set expectations, and address resistance with support channels in place.
Step 7: Go‑Live
Build a go‑live checklist: finalize configurations, migrate verified inventory, validate integrations, and provision hardware.Plan for a soft launch, starting with low‑volume days. Monitor KPIs in real time and ensure quick response teams for issues.
Choose adoption strategy—big‑bang (switch all at once) or phased—which aligns best with your risk tolerance and capacity.
Step 8: Post‑Implementation Support & Continuous Improvement
Monitor KPIs continuously—inventory accuracy, picking rate, labor utilization, and error frequency.Schedule regular system audits and updates—to deploy new features, track user feedback, and improve inefficiencies.
Provide ongoing support—implement a helpdesk or ticketing process with your vendor. Address bugs or workflow tweaks promptly.
Advance maturity gradually—incorporate optimization like task interleaving, slotting suggestions, and automated reporting over time.
5. How SendFromChina's Cloud WMS Helps Fulfillment
As a tech-powered 3PL operating from Shenzhen, Dongguan, SendFromChina (SFC) enhances cross-border fulfillment using its proprietary cloud WMS and a robust ERP backbone.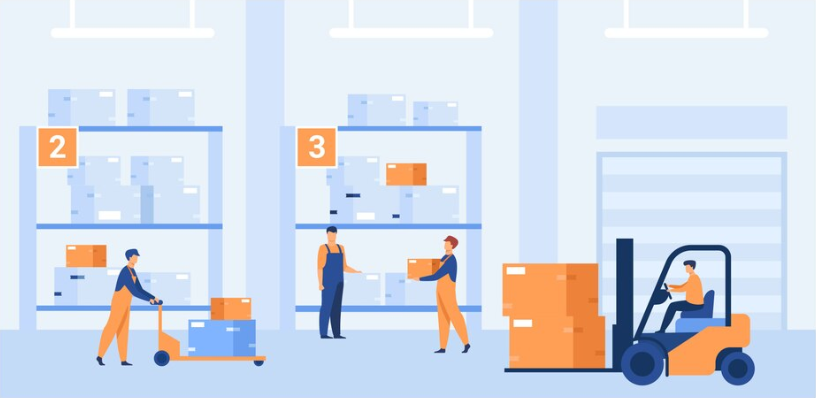
What makes SendFromChina’s WMS effective
End-to-End Real-Time Tracking: Integrates seamlessly with Shopify and other e‑commerce sites. Clients can monitor orders, inventory, and shipment statuses instantly.Free 60‑Day Storage Incentive: After signup, SendFromChina often offers complimentary storage for up to two months, reducing clients’ initial costs.
Value‑Added Services: Supports kitting, customized packaging, labeling, marketing inserts, battery processing, HS code assignment, and assistance with customs compliance.
Automated 3PL Fulfillment Model: Orders from multi-channel sellers are automatically received, processed, picked, packed, and dispatched via preferred DHL, FedEx, ePacket, or local courier routes.
Scalable Logistics Capacity: With over 40,000 m³ of storage and the ability to process over 500,000 parcels daily, SFC's WMS handles both SMBs and large crowdfunding campaigns.
Security & API Support: Secure storage facilities equipped with tracking cameras, along with a modern API suite for clients to integrate seamlessly into their own systems.
Proven Reliability: With over 17 years in cross-border fulfillment, and positive user reviews at major third-party platforms, SFC demonstrates consistent operational quality.
6. Conclusion
Cloud WMS offers a ground-breaking advantage for modern fulfillment. Businesses gain real-time insight, automated workflows, security, and close integration—all within a scalable, subscription-based model. With vendors like SendFromChina, these capabilities are combined with extensive Chinese logistics infrastructure to support cross-border sellers of all sizes. Migrating from on-premise to cloud WMS doesn’t just streamline operations—it positions your brand for tomorrow's global market demands.7. FAQs
1. What makes cloud WMS different from on‑premise WMS?
Cloud WMS is hosted off-site and accessed online—allowing real-time data access, subscription pricing, and automatic updates—unlike on-premise systems that need physical servers, IT overhead, and lagging data.2. Is cloud WMS secure for sensitive inventory data?
Yes. Leading providers use encryption, intrusion detection, regular backups, and disaster recovery. These security levels often surpass what small to mid-sized on-premise setups can afford.3. How quickly can we implement a cloud WMS?
A typical implementation—data migration, integration, staff training, pilot testing—can take anywhere from 4 – 12 weeks, depending on warehouse complexity.4. What features should I prioritize when choosing a cloud WMS?
Focus on real-time inventory tracking, order management, mobile access, system integrations, automation tools, analytics, labor optimization, and robust.5. Why choose SendFromChina’s cloud WMS for fulfillment?
You get China-based warehousing with seamless e‑commerce integration, expert value‑added services, free storage incentives, API-driven tracking, large-scale logistics capacity, and 17+ years of 3PL experience—it’s a powerful combination for global sellers.
Copyright statement: The copyright of this article belongs to the original author. Please indicate the source for reprinting.
Previous Post
FBA Fees Explained 2025: Fulfillment, Storage & Hidden Costs
Next Post
The True Cost of Kickstarter: 2025 Fees, Hidden Expenses, and Budget Tips
TAGS
Hot Research
Get a Custom China Fulfillment Solution with FREE Storage for 60 Days
Want to know about our services, fees or receive a custom quote?
Please fill out the form on the right and we will get back to you within a business day.
The more information you provide, the better our initial response
will be.