Table of Contents
Misshipment: What Is Misshipment and How To Prevent It
Time: Mar 04,2024 Author: SFC Source: www.sendfromchina.com
Understanding the nuances of misshipment and implementing strategic measures to prevent it are essential for businesses aiming to maintain high standards of service and reliability.

1. What Is Misshipment
2. What Are the Causes of Misshipment
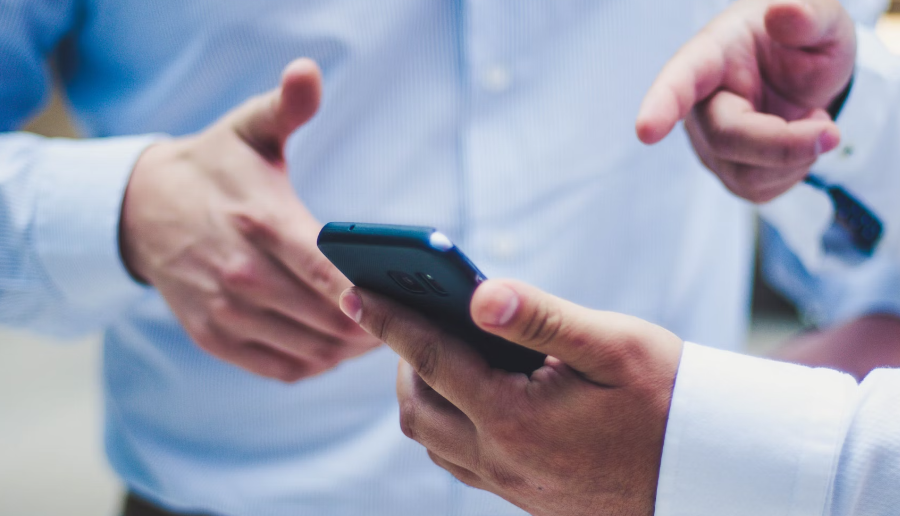
Picking Errors
Inventory Mismanagement
Poor Communication
Packaging and Labelling Mistakes
Rushed Orders and High Volume
3. How Does Misshipment Affect
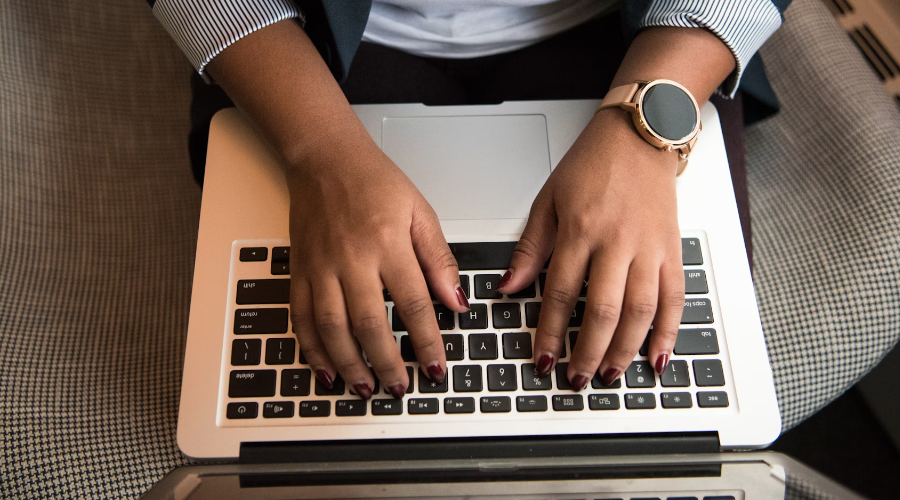
For Businesses:
Damaged Reputation: Customer trust and brand reputation can suffer greatly due to misshipments. In the age of social media and online reviews, negative experiences can be shared widely and quickly, potentially deterring new customers and eroding the loyalty of existing ones.
Inventory Discrepancies: Misshipments can lead to inaccuracies in inventory records, complicating inventory management. This can result in stockouts, where customers cannot purchase desired items because they are erroneously listed as out of stock, or overstock situations, tying up capital in excess inventory.
Reduced Efficiency: Dealing with the aftermath of misshipments distracts staff from their core duties, reducing overall operational efficiency. The time spent rectifying these issues could be better used in improving the business or focusing on growth initiatives.
Strained Supplier and Partner Relationships: Frequent misshipments may lead to tensions with suppliers, logistics partners, and retailers, potentially leading to strained relationships or even the termination of partnerships.
For Customers:
Loss of Trust: Customers expect reliability from the businesses they patronize. Misshipments can erode this trust, making customers more likely to turn to competitors in the future.
Unexpected Delays: Particularly for items needed by a specific date (e.g., gifts, essential goods), misshipments can cause significant inconvenience due to unexpected delays, affecting the customer’s plans or needs.
Financial Impact: In some cases, customers might face financial implications, such as missed work to return an item, non-refundable shipping costs, or the need to purchase a replacement item at a higher price elsewhere.
4. How to Prevent Misshipment
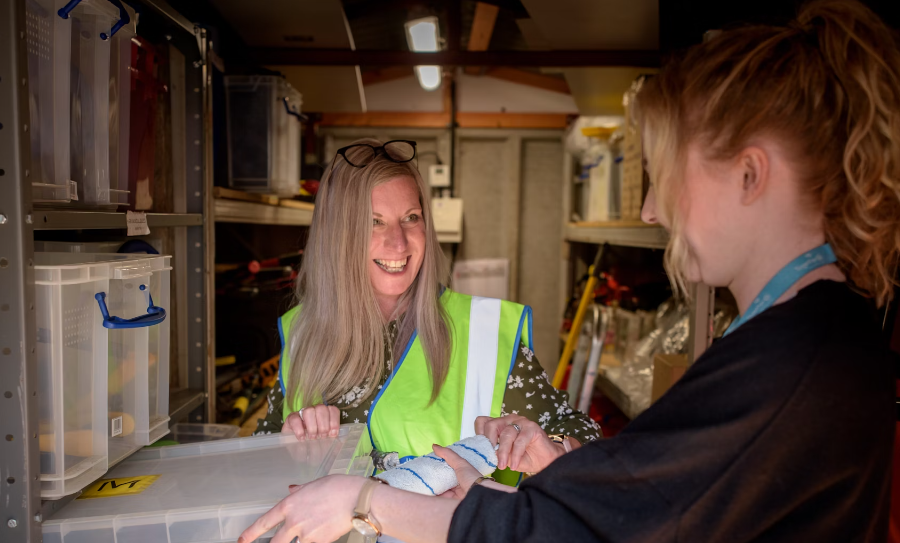
Regular Inventory Checks: Regular inventory checks is a critical measurement in preventing misshipments because they ensure that the physical stock in a warehouse matches the recorded inventory in the management system. Discrepancies between these two can lead to several issues, including misshipments, as employees may rely on inaccurate data when fulfilling orders. For example, if a product is erroneously listed as available in the system but is actually out of stock, an employee might pick and ship a different item as a substitute without realizing the mistake. Regular inventory audits help identify and correct these discrepancies promptly, ensuring that the inventory data is accurate and reliable. This accuracy is crucial for the proper functioning of automated systems and for employees who depend on this information to process orders correctly.
Utilize Barcode Scanner: Utilizing barcode scanners in the order fulfillment process is a highly effective strategy for preventing misshipment due to the accuracy and efficiency these devices bring to inventory management and order processing. Barcode scanners eliminate the need for manual data entry, which is prone to errors, by allowing workers to quickly and accurately capture product information directly from the barcode. This automation significantly reduces the chances of human error during the picking and packing stages. When an item is scanned, the warehouse management system (WMS) immediately verifies whether it matches the order details, ensuring that the correct product is selected. This real-time verification process helps to prevent misshipments by catching errors before the products leave the warehouse, thus maintaining high levels of accuracy in order fulfillment.
Upgrade Order Management System: Upgrading an order management system (OMS) is also a critical step in preventing misshipments, as it centralizes and streamlines the entire order fulfillment process, from receipt of the order to delivery. An advanced OMS integrates seamlessly with inventory management, warehouse management, and customer relationship management systems, ensuring that all departments have access to real-time, accurate information. This integration reduces the risk of errors at multiple points in the fulfillment process. For example, when an order is placed, the system instantly updates inventory levels, allocates stock for the order, and provides the warehouse team with precise picking information. By automating these steps, the likelihood of human error, such as selecting the wrong item or shipping an order to the wrong address, is significantly reduced. Furthermore, an upgraded OMS can automatically flag discrepancies or unusual orders for manual review, adding a layer of error prevention.
Keep Communication with Carriers: Carriers are responsible for the final step of the delivery process, and their performance directly impacts the accuracy and timeliness of shipments. By keeping in constant communication, businesses can relay important information about shipments, such as special handling instructions, delivery timeframes, or changes in delivery addresses. This reduces the risk of errors occurring during transit, which can lead to misdeliveries. Additionally, effective communication allows for real-time tracking and updates on shipment status, enabling businesses to proactively address any issues that may arise, such as delays or routing errors, before they result in a misshipment.
Outsourcing to Third-party Logistics (3PL): Outsourcing logistics operations to a third-party logistics (3PL) provider can significantly reduce the risk of misshipments due to the expertise, technology, and infrastructure these specialized companies bring to the table. 3PL providers are in the business of logistics and therefore invest heavily in the latest technology, systems, and processes designed to optimize the order fulfillment process. This includes advanced warehouse management systems, transportation management systems (TMS), and cutting-edge picking and packing technologies. These tools enhance accuracy and efficiency at every stage of the supply chain, from inventory management to shipping. By leveraging the capabilities of a 3PL, businesses can benefit from these investments without the upfront costs, ensuring that orders are fulfilled correctly and efficiently. Furthermore, 3PLs often have established relationships with a wide range of carriers, enabling more flexible and cost-effective shipping options, which can further reduce the risk of misshipments by selecting the most reliable and appropriate shipping methods for each order.
5. FAQs about Misshipment
1.What is the most common cause of misshipment?
2.How can technology help in preventing misshipment?
3.What role does staff training play in misshipment prevention?
4.Can implementing a quality control system guarantee the elimination of misshipment?
5.How should businesses handle misshipments when they occur?

Copyright statement: The copyright of this article belongs to the original author. Please indicate the source for reprinting.
Previous Post
Etsy Dropshipping: All You Need To Know About Etsy Dropshipping
Next Post
5 Steps To Set An Ideal Funding Goal For Your Crowdfunding Campaign
TAGS
Hot Research
Get a Custom China Fulfillment Solution with FREE Storage for 60 Days
Want to know about our services, fees or receive a custom quote?
Please fill out the form on the right and we will get back to you within a business day.
The more information you provide, the better our initial response
will be.