Table of Contents
How to Prevent and Fix Inventory Errors: The Ultimate Guide
Time: Sep 02,2024 Author: SFC Source: www.sendfromchina.com
Managing inventory is a critical challenge for e-commerce businesses. Inventory errors—like miscounts, incorrect SKUs, and lost items—can lead to financial setbacks, lost sales, and unhappy customers. To stay ahead in a competitive market, it’s essential to know how to prevent and fix these costly mistakes.
In this comprehensive guide, we’ll break down the most common types of inventory errors and provide proven strategies to maintain accurate inventory records. With these insights, you can improve operational efficiency, reduce costs, and enhance customer satisfaction.
Ready to perfect your inventory management? Let’s get started!
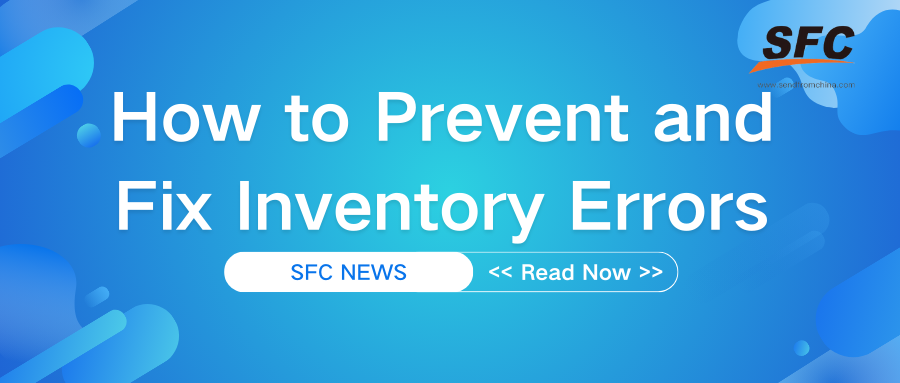
1. What Are Inventory Errors
Inventory errors occur when the recorded inventory data does not accurately reflect the actual stock available in a business's warehouse or storage location. The discrepancies can arise from various causes, including human errors, technological glitches, or procedural lapses. Inventory errors can lead to severe financial, operational, and reputational consequences for businesses, particularly in e-commerce, where inventory accuracy is crucial for customer satisfaction and operational efficiency.
2. What Are the Common Types of Inventory Errors
Understanding the different types of inventory errors is the first step in preventing and correcting them. Here are the most common types of inventory errors that businesses face:
Miscounted Stock
Miscounted stock occurs when there is a discrepancy between the actual count of inventory items and the recorded count in the inventory management system. It often arises due to manual counting mistakes, where employees may misread, skip, or double-count items during physical inventory checks. Miscounted stock can lead to incorrect reorder decisions, either overstocking or understocking, which affects the overall inventory management strategy.
Incorrect SKUs
Incorrect SKUs (Stock Keeping Units) involve mismatches in the labeling and categorization of inventory items. The error can happen if products are mislabeled or if the SKU system is not maintained properly. Incorrect SKUs can result in incorrect product shipments, customer dissatisfaction, and a negative impact on the business's credibility. It also complicates the inventory tracking process, making it challenging to know the exact inventory levels of specific products.
Data Entry Errors
Data entry errors are a common source of inventory inaccuracies. These errors occur when incorrect information is entered into the inventory management system. For instance, an employee might accidentally type the wrong product quantity or SKU number into the system. Data entry errors can cascade, causing multiple issues such as incorrect inventory counts, inaccurate financial reporting, and misguided inventory replenishment decisions.
Damaged or Lost Inventory
Damaged or lost inventory is another frequent type of inventory error. Products can become damaged during handling, shipping, or storage. Similarly, inventory can be lost due to theft, misplacement, or administrative errors. Failing to account for damaged or lost inventory skews inventory levels, leading to unexpected shortages and surplus inventory.
Incorrect Receiving
Incorrect receiving happens when the inventory received from suppliers does not match the purchase order in terms of quantity, quality, or specifications. It could be due to suppliers sending the wrong items or quantities, or due to errors during the receiving process. If not identified and corrected promptly, incorrect receiving can lead to inaccurate inventory records, affecting stock levels and customer orders.
3. How Do Inventory Errors Affect Your E-commerce Business
Inventory errors can have profound negative impacts on e-commerce businesses. These errors disrupt the entire supply chain, causing financial losses, customer dissatisfaction, and operational inefficiencies.
Financial Losses
Inventory errors often result in financial losses. For instance, overstocking due to incorrect inventory counts ties up capital in unsold goods, increasing storage costs and the risk of inventory obsolescence. Conversely, understocking leads to missed sales opportunities and lost revenue, especially during peak demand periods. Moreover, inventory inaccuracies can result in costly write-offs and adjustments.
Customer Satisfaction Issues
Inventory errors directly impact customer satisfaction. Incorrect inventory levels can lead to stockouts, backorders, and delayed shipments, frustrating customers and damaging brand loyalty. Inaccurate SKUs and product descriptions can cause customers to receive the wrong items, resulting in returns, refunds, and negative reviews. Maintaining accurate inventory is essential to ensure a seamless customer experience and foster trust and loyalty.
Operational Inefficiencies
Operational inefficiencies are a significant consequence of inventory errors. When inventory records are inaccurate, it disrupts the entire supply chain, causing delays in order fulfillment and increased labor costs due to repeated stock checks and adjustments. Additionally, inaccurate inventory data complicates demand forecasting and procurement, leading to poor decision-making and further exacerbating inventory issues.
4. How to Prevent and Fix Inventory Errors
To prevent and fix inventory errors, businesses must implement effective inventory management practices and leverage technology. Here are some strategies to help maintain accurate inventory levels:
Implementing an Automated Inventory Management System
An automated inventory management system is crucial for minimizing human errors and maintaining accurate inventory records. These systems provide real-time inventory updates, automate data entry, and offer predictive analytics for better demand forecasting. By reducing manual processes, automated systems significantly decrease the chances of miscounts, incorrect SKUs, and data entry errors.
Regular Inventory Audits and Cycle Counting
Regular inventory audits and cycle counting are essential practices for ensuring inventory accuracy. Physical audits involve counting all inventory items at once, while cycle counting involves counting subsets of inventory on a rotating basis. Both methods help identify discrepancies early and allow businesses to adjust their inventory records promptly. Regular audits also provide insights into inventory turnover rates and help identify slow-moving or obsolete stock.
Standardizing Receiving and Stocking Procedures
Standardizing receiving and stocking procedures helps prevent errors during the handling and storage of inventory. Implementing a consistent process for receiving goods, such as verifying shipments against purchase orders and inspecting items for quality, reduces the likelihood of receiving errors. Clear labeling, proper storage, and a systematic approach to stocking inventory further minimize the chances of misplaced or damaged goods.
Training Staff on Proper Inventory Management Techniques
Proper training is essential for preventing inventory errors. Staff should be trained on inventory management best practices, including accurate data entry, proper handling and storage of inventory, and conducting physical counts. Regular training sessions and refresher courses help keep staff updated on the latest procedures and technology, reducing the risk of human errors and enhancing overall inventory accuracy.
Utilizing Real-Time Inventory Tracking
Real-time inventory tracking technology, such as barcode scanners, RFID systems, and IoT sensors, enables businesses to monitor inventory levels continuously. These technologies provide instant updates to the inventory management system, ensuring accurate and up-to-date stock information. Real-time tracking also helps identify discrepancies and potential issues promptly, allowing for quick corrective actions.
Addressing Discrepancies Promptly
Addressing inventory discrepancies promptly is critical to maintaining accurate inventory records. When discrepancies are identified, it's important to investigate the root cause and implement corrective measures immediately. Whether it's a miscount, data entry error, or receiving mistake, addressing issues quickly prevents them from compounding and affecting other areas of the business.
5. Get Started With SFC Services
SFC stands at the forefront of order fulfillment with cutting-edge facilities in Shenzhen, China. Utilizing sophisticated software, we specialize in seamless and trustworthy fulfillment solutions for ecommerce, dropshipping, and crowdfunding platforms. At SFC, we are dedicated to accelerating your business growth through secure warehousing, efficient processing, customizable packaging options, and adaptable shipping strategies while saving you time and money.
Whether you have or do not have a fulfillment partner, particularly your products manufactured in China, you should consider SFC. Click the button below and get help from SFC logistics experts.
What Makes SFC Special
Over 17 Years of 3PL and Order Fulfillment ExperienceAll-in-one Tracking Number
Popular Platform API Integration
30 Days of Free Storage
No Hidden Fee
Custom Packaging
Worldwide shipping solutions
Value-added Services
6. FAQs
How often should I perform inventory audits?
Inventory audits should be performed regularly, depending on the size and nature of your business. For most e-commerce businesses, a combination of annual physical audits and regular cycle counting (monthly or quarterly) is recommended to maintain inventory accuracy.
What are the best tools for inventory management?
The best tools for inventory management include automated inventory management software, barcode scanners, RFID systems, and real-time tracking technologies. These tools help streamline inventory processes, reduce manual errors, and provide accurate inventory data for better decision-making.
How can technology help in reducing inventory errors?
Technology helps reduce inventory errors by automating manual processes, providing real-time inventory updates, and improving data accuracy. Automated systems minimize human errors, while real-time tracking technologies ensure inventory levels are continuously monitored and discrepancies are identified promptly.
What is the difference between cycle counting and physical inventory counts?
Cycle counting involves counting a subset of inventory on a rotating schedule, while physical inventory counts involve counting all inventory items at once. Cycle counting is less disruptive and can be performed more frequently, making it an effective method for maintaining inventory accuracy without halting operations.
Can inventory errors be completely eliminated?
While it is challenging to eliminate inventory errors completely, businesses can significantly reduce them through effective inventory management practices, regular audits, staff training, and technology adoption. Continuous improvement and proactive measures are key to minimizing errors and maintaining inventory accuracy.

Copyright statement: The copyright of this article belongs to the original author. Please indicate the source for reprinting.
Previous Post
Crowdfunding Prelaunch: Why You Need It for Your Crowdfunding Campaign
Next Post
TAGS
Hot Research
Recent News
Get a Custom China Fulfillment Solution with FREE Storage for 60 Days
Want to know about our services, fees or receive a custom quote?
Please fill out the form on the right and we will get back to you within a business day.
The more information you provide, the better our initial response
will be.